What is Predictive Maintenance?
Definition
Predictive maintenance (PdM) is a proactive maintenance strategy to reduce the likelihood of equipment failures by forecasting when issues might occur and addressing them systematically.
This strategy uses sensors to capture equipment performance data so maintenance frequency to be as low as possible without risking unplanned downtime.
Why it Matters
Under a PdM program, maintenance is only performed when it is required instead of on a static schedule like traditional preventative maintenance. This proactive strategy helps operators balance operator productivity and equipment reliability.
Benefits of predictive maintenance include:
- Reducing operational costs by minimizing the time to maintain equipment and the cost of spare parts and supplies.
- Lowering necessary capital investment reserves by extending the useful life of equipment
- Improving tenant comfort by avoiding disruptive events before they occur
Enertiv’s predictive maintenance software predicts failure and provides notifications to maintenance staff, which helps to remotely manage assets in the most cost efficient way.
How it Works?
Predictive maintenance combines equipment monitoring sensors and predictive models.
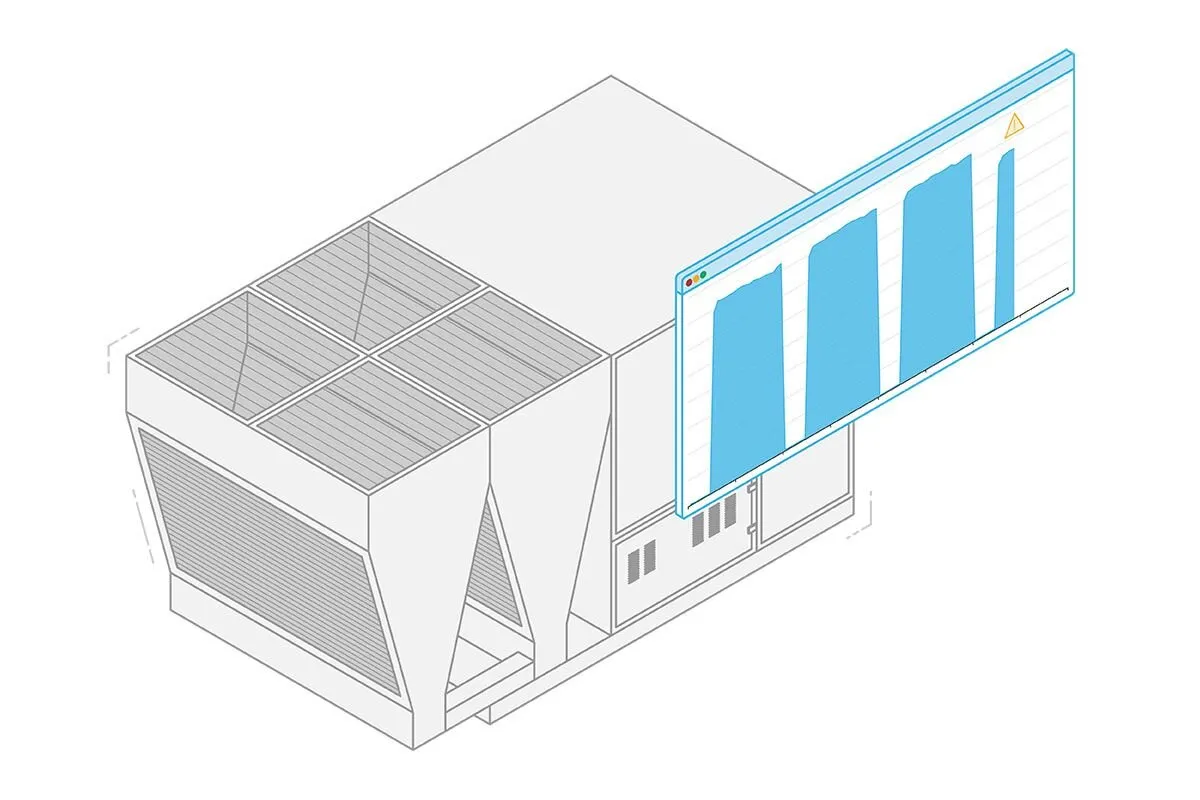
- Equipment monitoring sensors
Equipment data can take multiple forms including: electrical demand, temperature, pressure, vibration and tank levels. This data serves as the foundation of predictive maintenance models.
- Predictive Model
The data collected by sensors is analyzed using predictive algorithms that identify trends to detect equipment faults before they occur. Enertiv’s algorithms are powered by 10 billion hours of equipment-level performance data. This enables AI models to identify subtle abnormalities and patterns that could not be found with human capabilities.Predictive Maintenance vs. Preventive Maintenance
Predictive Maintenance vs. Preventive Maintenance
Predictive Maintenance
- Predict failure of a piece of equipment before it happens
- Prediction based upon the equipment condition, which is evaluated by the data captured by the equipment-monitoring sensors
- Ensures a piee of Equipment requiring maintenance only shut down right before imminent failure
- 10% more cost-effective than preventative maintenance
Preventative Maintenance
- Maintain equipment up and running based on routine maintenance tasks
- Prediction based on calendar schedule or equipment usage level
- Relies on present planning. It does not take into account the asset wear which means there might be excessive maintenance on some asset
- 12%–18% more cost-effective than reactive maintenance