How to Overcome Unexpected CapEx Risk
An unexpected capital expenditure for an equipment replacements is one of the biggest risks facing owners and asset managers. In this video, Subhan Mansoor, a Client Success Manager at Enertiv, explains why the current process is prone to inaccuracies and how technology can lead to better projections and ultimately better cash flow.
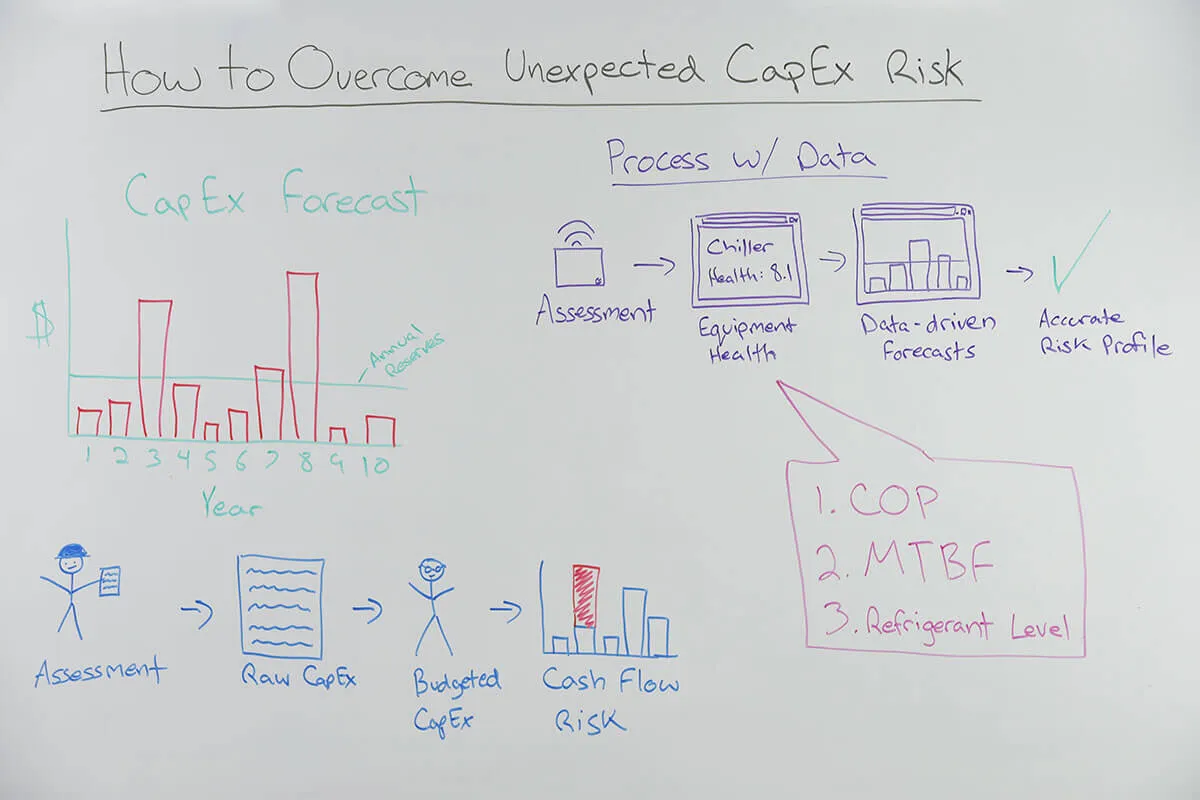
Video Transcript
Hello, my name is Subhan Mansoor, and I’m a Client Success Manager at Enertiv and today, in this video, I will be talking about how you can overcome unexpected CapEx risk.
First, we’ll be going over why it’s so necessary to accurately forecast your CapEx investments 10 or 20 years down the line. Second, we’ll be seeing how forecasts are made in the status quo and how the process could be improved by leveraging technology such as IoT sensors.
Let’s first talk about the benefits of accurately predicting your CapEx investment by walking through an example. In this case, you have big CapEx investments in year three and year eight. Suppose the year eight investment is reflective of a boiler replacement that you have installed 10 years ago and is going to be due for a replacement in year 18. What if that CapEx investment gets transported to year three, because the boiler fails prematurely? This is a case we’ve seen across many portfolios.
How can this risk be mitigated and avoided, and what are the benefits of accurately predicting this? Well, all the money that you’ve artificially locked up in the replacement of a chiller or boiler or any heavy piece of equipment, could’ve been invested elsewhere to realize better returns. Having a more accurate project also enables owners and asset managers to be much more confident going forward in terms of the assets installed in your real estate portfolio.
Today, the process starts with an on-site engineer who is running certain reports that are archaic in their data collection methodology. The methodology is inaccurate because they’re not pulling data from dynamic sensors, they’re relying on a snapshot value of certain metrics that are informing a poorly documented raw CapEx that makes its way into the cash flow risk profile.
Once you install IoT sensors and start leveraging technology of the 21st century, you see a much different picture. How? Because you can give a quantifiable metric to the health of your piece of equipment. Let’s talk about this more with a specific example to ease understanding.
We’ll take a one-thousand-ton chiller that costs $200,000 to replace. That’s a huge number and we want to be as accurate as we can in terms of either scheduling out a major repair or completely replacing it at the end of its lifetime. Now, in this case, we can use these three metrics to accurately come up with a number that quantifies the chiller’s health.
The first one would be the coefficient of performance. The coefficient of performance is the efficiency of the chiller. It’s a measure of how much energy the chiller consumes to bring about a certain change in the supply and return water temperatures. Now, by installing a couple of sensors on the supply and return side of the chiller, while simultaneously monitoring the power draw, you can dynamically come at a coefficient of performance which tells you how efficiently your chiller is running.
As the equipment gets older, you’re going to see that COP coming down. And if you’re monitoring that more directly and more dynamically, you’re getting a much more accurate picture than you were getting of the same equipment from disparate sources that could be prone to error as we discussed.
The second one would be the MTBF, or the mean time between failure. As the name implies, this is quantifying how long your chiller runs before it requires a major repair. If this number is squeezing, you can tell if there’s something wrong with your chiller and that you need to start investing in preventative maintenance in order to ensure that your equipment does not fail prematurely. Not only are you accurately predicting when you’re going to invest in this chiller, you’re also prolonging the life based on data-driven preventative maintenance practices.
That fits neatly into the third point, which is refrigerant levels that could potentially be picked up by installing power draw on the circuits that allow us to see how fast the chiller is turning and off. If the chiller beings short cycling, turning on and off more than 11 times in a given hour, then probably you need to check your refrigerant levels, or the temperature set points, so your chiller runs more smoothly. Doing this prolongs your CapEx investment and thereby the time value of money, and also enables you to step confidently into the future knowing exactly when your real estate assets that cost hundreds of thousands of dollars are going to require replacement.
This is how we can step away from a manual process that is prone to inaccuracies towards the more innovative methodologies that use all these sensors to mitigate the risk profile of the portfolio knowing exactly what their equipment and asset health looks like.
We only talked about the chiller in this example, we could do the same analysis on more equipment like boilers, like PTAC units, and more. So, if you have more questions regarding those, feel free to contact us, my name is Subhan Mansoor. Again, I hope you enjoyed the video and that you learned something from today’s session.