Blueprint for Success: Streamline Workflows
Recently, we released a white paper entitled Blueprint for Success: the 5 Steps to Digitizing Building Operations and Improving Returns at Scale.
The point of these videos, and the white paper that they’re based off of, is to explain as clearly as possible exactly what owner and operators can expect when deploying technology to streamline their building operations, reduce operating expenses and ultimately increase the value of their assets.
In this video, Comly Wilson explains why we need to rethink the value of data and technology as an enabler, not as a solution itself.
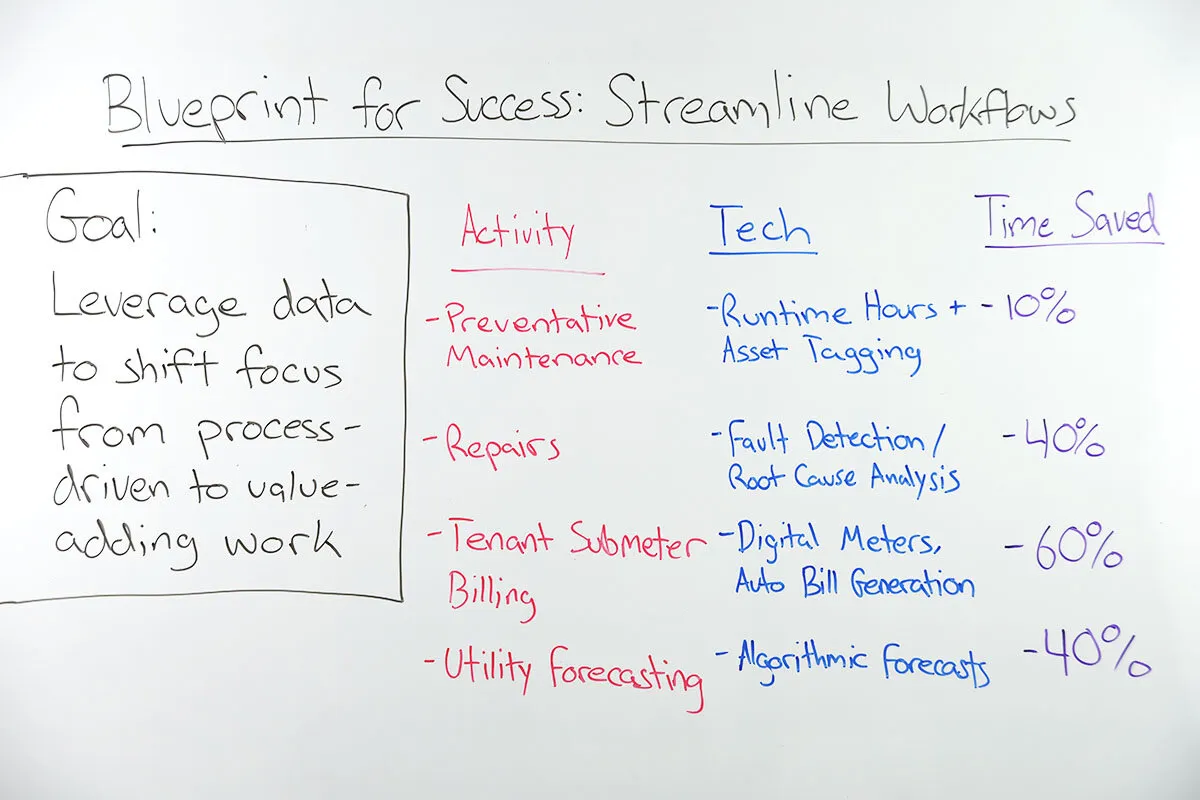
Video Transcript
Hi, my name is Comly Wilson and welcome to the second Blueprint for Success Video. Now the point of these videos, and the white paper that they’re based off of, is to explain as clearly as possible to owners and operators exactly what they can expect when deploying technology to streamline their building operations, reduce operating expenses and ultimately increase the value of their assets.
In the first video, we talked about data collection and how you can’t just rely on building management system data, you also have to deploy targeted IoT sensors, and soak up as much qualitative information about the asset and the equipment within that asset as possible.
But now we can get onto the fun stuff, what to do with all that data.
There’s an assumption that data translate to energy savings, and that’s really where the value comes in, but that’s like saying to be an Olympic athlete, you just need a good diet, it’s obviously an important part of the equation, but it’s not everything.
We want you to rethink technology, we want you to first think about technology as an enabler, not as a solution itself. So, the goal at this step is to leverage that data to shift from process-driven work to value-adding work.
The way we do that is by tackling all of the manual, reactive and time-consuming processes that are currently taking place in building operations. There’s a laundry list and we’ll only cover a few of them.
As an example, preventative maintenance is largely based off calendars, static calendars that take assumptions into how much each piece of equipment is being used. But the data we’re collecting will tell you the real runtime hours of equipment, meaning you don’t have to do as much as maintenance as you think you do. You can save about 10% of the time that you’re spending on calendar-based maintenance by shifting to a runtime hours-based approach.
Now, preventative maintenance is great, but you can’t stop every piece of equipment from failing. When it comes to repairs, it often takes a very long time to find the root cause of an issue. For example, say the chiller went down, it’s often not because the chiller is broken, it’s because the water cooling tower doesn’t have enough water in it. And that’s because the booster pump down the line had a motor malfunction. Now, it could take a very long time for an operator to get to the root cause of the issue, but with that data and with targeted alerts, you can have your operators go directly to the source of the problem, saving a lot of time, and allowing them to focus on more value-adding work.
And again, a lot of portfolios are still sending engineers to each tenant space to write down submeter consumption data each month. This is time consuming; not only are they writing it down on pen and paper, they have to transmit it to accounting, who has to compile spreadsheets. This can all be streamlined with digital meters and automated bill generation.
But it’s not just the on-site teams that are spending a lot of time on this process-driven work. There’s also the asset managers, who have to do utility forecasting to accurately predict budgets for the next year and even within the year. Say you have 6 months of data, often you’re just adding the data from last year for the next six months. Not only is this time consuming, it often is incorrect. So you want to use that data that we collected in the first step, and apply algorithms to make a more accurate forecast. And save time.
The list can go on and on, but the point is, that you want to think about technology as an enabler because the time that you save is more valuable than all the energy savings in the world.
In the next step, we’re going to talk about implementing insights, many of which can be energy savings, but first, we want to focus on tackling those tedious, manual, and reactive processes.
So, thanks for listening and stay tuned for the next video.