Why Non-sensor Data is Critical to Smart Buildings
Smart buildings depend on real-time sensor data. But without context, that sensor data is basically useless.
In this video, one of Enertiv's software engineers, Eric Blum, explains how nameplate information, operations manuals, maintenance schedules, and pictures can be leveraged to deliver much more specific insights.
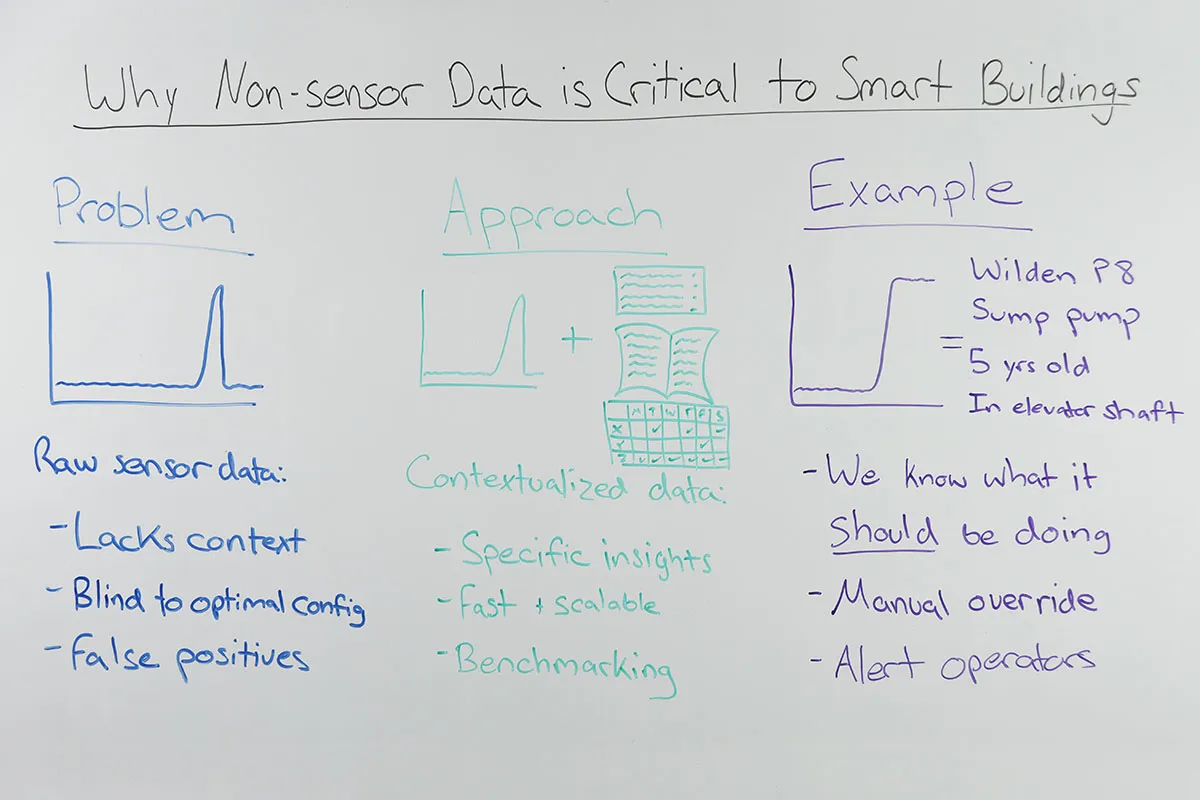
Video Transcript
Hey there, my name is Eric Blum, I’m a software engineer at Enertiv, and I’m here to tell you why non-sensor data is critical to smart buildings.
One of my big jobs at Enertiv is to look through the billions of hours of machine performance data that we have and find actionable insights for our operators. But if we’re just looking at the sensor data by itself, this is very difficult, we have too much data to look at manually, and without the context to tell us what equipment this is and how it should be operating, we just can’t really say.
If I showed you this graph, can you tell me if the baseline is bad? Is the spike here bad? We just can’t know.
We’re blind to the optimal configuration of this device, so we don’t know how this equipment should be running and we can’t really say for sure if this is the right way to do it. This leads to false positives, which is antithetical to how smart buildings should work because it erodes the confidence of the technology and wastes the time of your operators, which is a big problem. But how do we build the context around this sensor data?
That’s where non-sensor data comes in. The approach is to gather stuff like the nameplate information to tell us what size of pump or elevator motor this is; to collect the operations manual to tell us how you fix it if something goes wrong; to collect the maintenance schedule to tell us when it should be going down and coming back up; to collect a picture of it, so we can see where it is located in the building.
When we collect all that information, you can make much more specific insights about the sensor data that you see. Because now you know what’s optimal based on what type of equipment it is, you can say when it really goes down.
This is fast and scalable because you don’t have to re-write every model for every new building you go to. You can just build a model based on, this is how pumps should work, this is how elevators should work, and you’re able to say, with high confidence, that they’re going down, or that they need maintenance.
You’ll also be able to benchmark your equipment. Which equipment are under performing? You don’t know that if you don’t know what kind of equipment they are.
So here we have an example where we’ve combined the sensor data and the non-sensor data. We’re able to say, because of the non-sensor data, that this is a sump pump, Wilden P8, it’s five years old, in the elevator shaft.
Now, just this sensor data, it might be hard to say what’s going on, but now we know it’s a sump pump. It goes online, but stays on, that tells us that it could be a very bad thing, it could be the basement flooding, which can lead to massive damage to your building. Instead, we were able to send a very specific insight, with high confidence, directly to the operator and they can fix it right away.
In this case, they had manually overridden the automatic operation of the sump pump, so the basement wasn’t flooding, but the pump was running without any water in it, which causes damage to the pump. Because of what we knew about how the pump should work from the non-sensor data, we were able to give a very quick, very high confidence alert to the operator and they were able to save their equipment before it broke down.
I hope this shows how important it is to combine your sensor data and non-sensor data to really complete the picture.
Thanks for listening, my name is Eric Blum.