For most asset managers, “maintenance and repairs” is no more than a line item on the P&L that increases a small percentage each year. This is understandable, if costs stay reasonably close to the assumption, most asset managers don’t mind being spared the details of how it is spent. More surprisingly, the details of what drives maintenance costs are also largely a mystery for the operations managers and engineers responsible for the building systems being maintained.
The impact of maintenance practices extends far beyond a share of operating expenses. Ineffective maintenance can negatively affect the tenant experience to the point of influencing leasing decisions. Equally as bad, improper maintenance can shorten the life of equipment, leading to large capital expenditures not sufficiently covered by reserve funds.
To reduce operating expenses, diminish risk, and ensure tenants receive what they’re paying for, maintenance practices should be proactive and transparent. Unfortunately, most operators do not have the necessary tools to make this reality. Here are the biggest problems with real estate maintenance today and how technology can help alleviate these challenges.
1. Calendar-based Preventative Maintenance
Preventative maintenance (PM) costs significantly less than running equipment to failure and making ad hoc repairs. Despite this, many real estate companies still do not perform regular preventative maintenance. Even for the portfolios that do, there are inefficiencies that drive up the cost and limit the effectiveness of PM programs.
When PM schedules are planned, the frequency of maintenance on individual pieces of equipment is largely derived from the manufacturer’s recommendations. These recommendations are built on assumptions and rules of thumb that rarely match reality. For example, there are often primary and secondary hot water pumps, yet many PM programs call for the same amount of maintenance even though one piece of equipment experiences significantly more wear and tear.
How to fix this
A better approach is to leverage sensor data and translate that information into runtime hours. From there, a preventative maintenance schedule can be created based on how much the equipment is used rather than an amount of time that has passed. There are consequences of both over and under-maintaining equipment, this strategy guards against both.
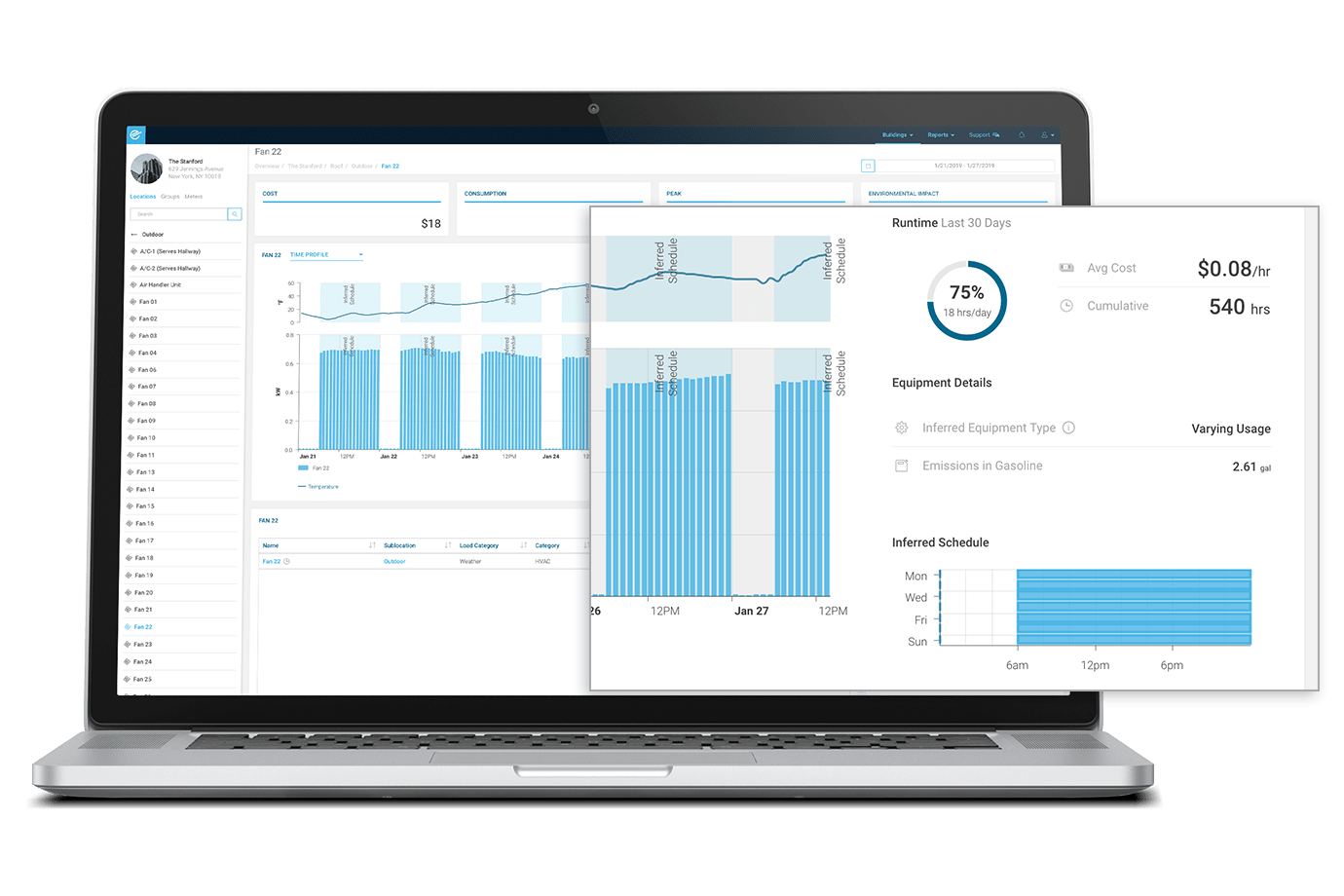
2. Maintenance Transparency
Creating a maintenance schedule is only the first part. Getting operators and third-party vendors to be accountable to the plan is another story.
On-site operators are usually busy resolving the various issues that arise throughout the day. When there are fires to put it, routine maintenance tasks get put off, ironically setting the stage for more emergencies down the road.
There’s another, more insidious, example of costs rising due to lack of transparency. In many cases, third-party maintenance vendor’s incentives are misaligned with the landlord’s. Preventative maintenance does not take very long, and most contractor’s businesses are not sustainable on PM alone. On the other hand, repairs take a lot longer, which allows vendors to charge more. The less maintenance performed, the more breakdowns, which means more income. This perverse incentive often takes place because there is no way for the owner to verify the work that is being done.
How to fix this
One way to add transparency is to map work orders onto equipment performance data. From there, any discrepancies in reported hours or even missed PM could be flagged and brought to light. Usually, the knowledge that there is accountability is enough to overcome misaligned incentives.
3. Work Order Logging and Archives
Assuming operators and maintenance vendors are executing the PM schedule as laid out, it can still be a challenge to archive and analyze logged work orders in any meaningful way.
Most logging is still done with pencil and paper. If logs are stored at all, they are in binders or maybe scanned into digital PDF documents. In some cases, stickers are placed on equipment with the date of previous maintenance. Obviously, this is not the optimal way to pass information.
Work orders are incredible sources of data that can inform future capital investment decisions and help illuminate the potential efficiencies. But this is impossible if the data is stored in flat files or in hard copies.
How to fix this
CMMS software has existed for some time to bring routine maintenance tasks online. These are powerful tools and a great first step. Well-designed solutions will be able to integrate work order logs with equipment performance data to add independent verification and quantify the ROI of maintenance.
4. Unexpected faults
Even the best PM program cannot avert most equipment breakdowns. That’s because 82% of equipment failures occur in a random pattern, instead of based on the time since the previous repair or maintenance.
A random pattern does not mean that it’s completely random, however. It just means that equipment faults result from events unrelated to how much time has passed. These random malfunctions can occur because fan belts slip off motors, refrigerant leaks, a jam in a mechanical system or any number of events.
In most cases, these faults go undetected until the effects become obvious and tenants complain to the property manager. This delay in addressing the issue leads to unnecessary wear and tear, a worse tenant experience, and the kinds of emergencies that take operators away from routine maintenance.
How to fix this
Equipment performance data used to optimize preventative maintenance can also be used as fault detection. Alerts sent to operators as soon as a fault occurs has been shown to reduce mean time to repair (MTTR) by as much as 600%.
5. Environmental issues
Not every issue that operators deal with is related to equipment. There are a range of environmental problems that can spring up unexpectedly and cause significant damage.
One common example is leaks and/or flooding. Maintenance may include checks on the plumbing infrastructure, but it is often very difficult to predict when and where issues will occur. This is both common and expensive; insurance claims that involve water damage cost three times as those that do not and make up half of all insurance claims submitted.
How to fix this
Sometimes floods can be avoided in the first place, such as those resulting from frozen pipes bursting. In these cases, software connected to temperature sensors can notify operators well before the pipes reach freezing so that corrective actions can be taken. In other cases, moisture sensors can detect a leak as soon as it occurs so the worst damages can be prevented.
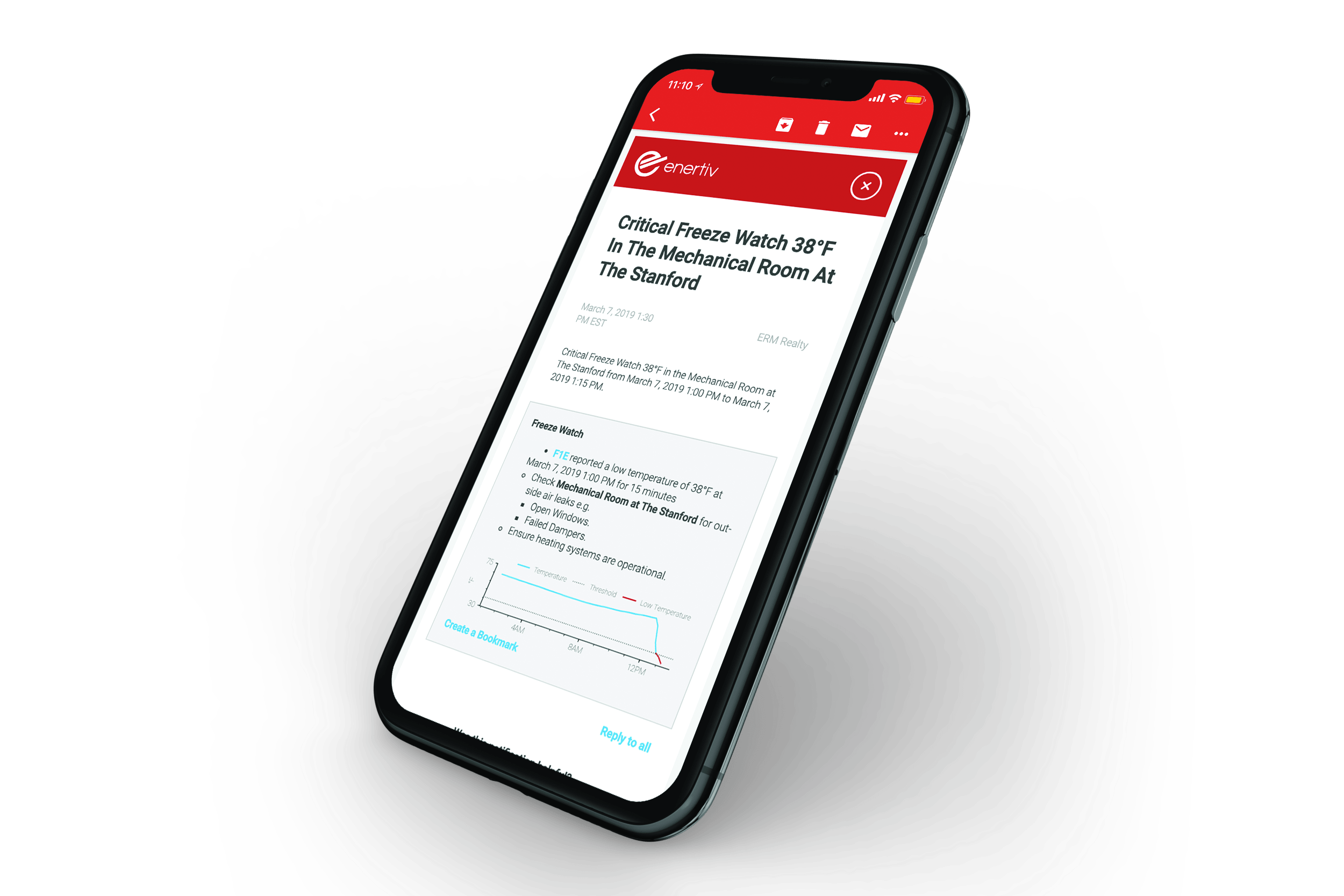
6. Troubleshooting
When equipment does fail, the operators on site are the first line of defense. But they often don’t have the skills necessary to troubleshoot complex pieces of equipment such as boiler or chiller plants.
For problems that are too technical for the on-site team, the operations manager is often called on to assist. Despite being highly capable engineers, supporting dozens of buildings, each with their own personnel, infrastructures, and idiosyncrasies, is a significant challenge.
If the equipment fault cannot be resolved over the phone, the operations manager may have to travel to the site to evaluate the equipment in person. These managers are some of the busiest professionals in commercial real estate, any time spent in transit is time they are not spending on more value-add activities.
How to fix this
Even with fault detection, it can be difficult for an operations manager to troubleshoot issues remotely. Nowadays, these experienced operators can leverage a “digital twin” to remotely access the equipment in question, along with the equipment nameplate information, real-time analytics, and maintenance history to assist with troubleshooting without traveling to the site.
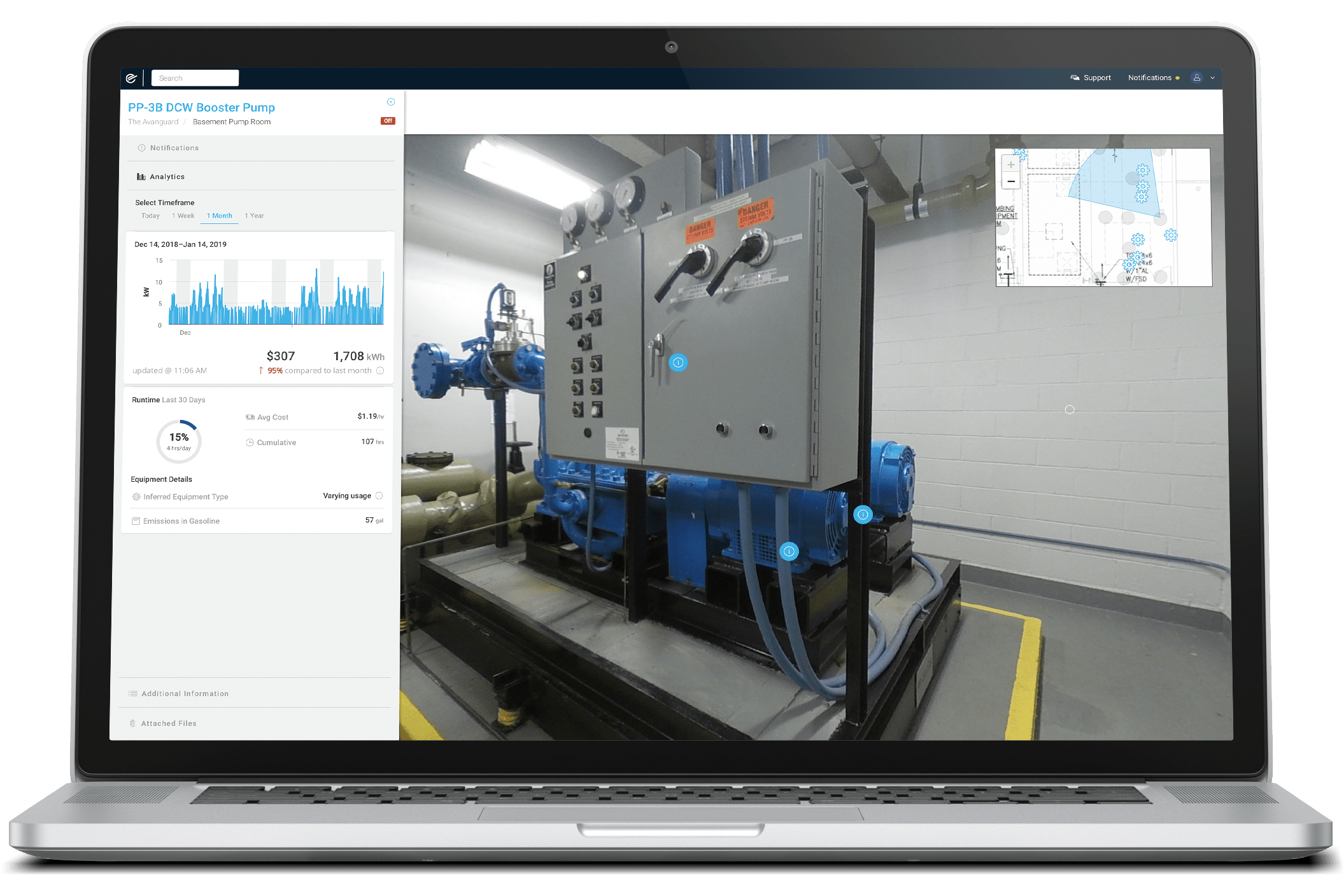
7. Documentation
Another helpful tool when troubleshooting are the O&M manuals, spec sheets, and riser diagrams of the equipment and mechanical rooms. In most cases, if this documentation exists, it is stored in a drawer in the chief engineer’s office and nowhere close to where it is needed when problems arise.
How to fix this
The same digital twin that can enable remote troubleshooting can be used as a documentation repository. With a digitized and centralized source of information, the details about specific equipment and related infrastructure can be easily searchable for anyone in the organization.
8. New Operator Training
As important as documentation is today, it is becoming increasingly more so each year. That’s because experienced operators are aging out of the workforce and there simply isn’t the labor stock to replace them.
Case in point, 70% of trade workers are over 45 years old and 30% are over 55 years old. To make matters worse, twice as many high school graduates are going to university rather than technical schools or directly into the workforce.
This means that the personnel who will responsible for operating buildings will have to get more done with less training. This applies to third-party management companies as well, and getting less experienced operators up to speed quickly is becoming a big challenge. There are systems that are prone to failure, unique configurations and complicated equipment relationships that can’t be explained with riser diagrams alone.
How to fix this
The digital twin can be a powerful tool for reducing the time it takes for a new operator to get up to speed on the intricacies of the building and future proofing the organization against the looming skill gap.
9. Assessments
Periodically, real estate companies will perform a comprehensive assessment of their equipment to determine what needs to be repaired and to predict upcoming capital expenditure needs. Some portfolios will only do this near a disposition, but some sophisticated portfolios do this quarterly.
Either way, performing a full assessment takes a lot of time, and usually must be done by experienced, high-value personnel. Moreover, there is no guarantee that the predictions made are accurate. Operators are largely limited to what they can hear, smell, feel and see and they are just as susceptible to biases and other judgement flaws as any other human.
The capital expense predictions made by the engineers permeate throughout the company, even into the cash flow analysis for the brokers and asset managers. Spending a lot of time and money to make high-stake predictions that may not be accurate is clearly not ideal.
How to fix this
It comes back to equipment performance data, but not for the real-time analysis that benefits maintenance and repairs. Historical performance data must be fed into a centralized database with the make, model and specs. This significantly reduces labor hours required and delivers more consistent assessments.
10. CapEx Decisions
Assessments are not done for their own sake. The goal is to enable asset managers to come up with expected capital expenditures for the foreseeable future and to back out a required CapEx reserve number for each year.
Assuming equipment assessments were accurate, and replacements come due when expected, there’s still the question of which equipment to purchase.
Left up to the asset manager, the decision would likely be on the equipment with the lowest upfront cost. The chief engineer on the other hand would likely choose equipment with the best reputation. Neither of these approaches are ideal when taking the long-term interest of the portfolio into account.
How to fix this
The centralized database that assessments are fed into can also be used to benchmark different makes and models against each other. This “equipment-level benchmarking” can expose the true lifetime costs of operating equipment including both utilities as well as maintenance and repair costs. Asset managers are always looking for more data-driven approaches, but simply don’t have the tools in most cases.
Want to bring data and transparency to your organization? Schedule a demo of Enertiv’s building operations platform today!