For many operators in commercial real estate portfolios, it’s a struggle to find the time to plan and implement a comprehensive maintenance plan. Ironically, this is often because they are dealing with unscheduled emergencies so often that they can’t take a step back. In most cases, under-maintaining assets leads to a “debt” that is impossible to recover from. Worse, this reactive maintenance process relies on tenant complaints for fault detection, which means the problem likely has been occurring for days or even weeks.
Operators (often justifiably) complain that creating a proper maintenance schedule costs time, money and labor resources that they simply don’t have. The paradox is that it costs much more in the long run to not have any strategy in place. Building inefficiencies and wasted maintenance staff time usually add up to significantly more than taking the upfront time to put a system in place.
Unfortunately, even when there is time to plan, the process for doing so is prone to errors. The equipment manufacturers’ suggested maintenance schedule is often based on usage (for example, the number of trips an elevator takes); it is the operators job to estimate the time intervals between usage thresholds without access to reliable data. This is obviously susceptible to both over and under estimation. What results is a non-specific, word-of-mouth strategy.
This is the root cause of maintenance debt: most teams simply don’t have an operations performance system in place. Without one, there are likely too many or too few tasks scheduled per piece of equipment, there is improper maintenance staff prioritization and teams spend too much time responding to work orders than scheduled maintenance.
When Even the Best Plans Go Wrong
The alternative, for those that can afford it, is to implement preventative maintenance schedules for all equipment systems across all managed buildings. While this is a better strategy, it can be costly and sometimes leads to an unnecessary waste of maintenance staff time by scheduling too many scheduled checks. Left unattended, over-maintaining silently and continuously squanders precious labor resources.
According to the International Facility Management Association (IFMA), the CRE industry has been conservative in its approach to setting preventive maintenance intervals. In some portfolios 80% of preventive maintenance costs are spent on activities with a frequency 30 days or less.
The specific maintenance activities are also subject to scrutiny, the IFMA also found that 30-40% of preventive maintenance costs are spent on assets with negligible failure impact. This adds up to an estimated 18-30% wasted for every dollar spent on maintenance. One specific example found that maintenance operations were wasting up to 25% of available labor and that up to 60% of this waste results from activities that add no value to the performance of the building.
In the well-established world of Lean Manufacturing, waste is defined as “anything that adds no value to the manufacturing process.” Most practitioners of the lean methodology would be appalled to learn how most preventative maintenance programs are run in CRE.
Some examples of waste familiar to most building operators include: waiting for tenants to complain, spending time searching for the root cause of a problem, making multiple trips to bring the right tools for a job and performing preventative maintenance when it is redundant or unnecessary.
Lean manufacturing proponents argue that a relatively small number of inventory items account for the major part of the total inventory value. When applied to maintenance activities a similar pattern is seen. The IFMA found that 70% of preventive maintenance costs were incurred by 25% of activities and just under half of the activities accounted for 90% of Preventive Maintenance costs.
The Goldilocks Zone of Maintenance
Whereas under-maintaining assets is characterized by activities not performed and relatively obvious equipment failures, over-maintaining is characterized by performing preventive maintenance activities that leave a less obvious waste trail. Most operators with a robust preventative maintenance plan are inclined to believe that their activities are effective. However, when left unchallenged there is simply no way to know the impact on maintenance labor costs and the profitability of a property.
In many properties, maintenance activities have been established over time with little technical discipline supporting the decision process. But the question remains, how are building operators supposed to predict the onset of equipment issues, detect existing failures or adjust components before failure occurs?
Until recently, maintenance frequencies based on personal judgement are heavily influenced by monthly and annual calendar cycles. The IFMA found that if each of these frequencies was extended by just one week, most facilities could realize a 20% reduction in the direct cost of their preventive maintenance program.
This is especially important given the fact that over-maintaining adds little or no value to the detection or prevention of asset failure. It is often assumed that the probability of failure reduces with increased preventive maintenance frequency. However, the relationship between preventive maintenance frequency and the probability of failure is not so tightly correlated.
Especially in cases where assets are opened, adjusted, or otherwise handled, there is a chance that equipment will be returned to service in a worse condition than when it was received. This means that as maintenance frequency increases, the probability of a maintenance-induced failure also increases.
Dynamic, Data-driven Maintenance
The challenge associated with changing maintenance frequency is that without accurate data, it is difficult to know where the current frequency sits on the over/under scale. Frequency reductions could result in proportional reductions in equipment reliability. To add to the risk, the results may not be apparent for some time. Without specific, real time data, the only reasonable strategy in changing maintenance processes are where the consequences of failure are low and the current frequency is obviously high. This conservative approach will never lead to significant improvements or increased returns.
Instead, operators should be looking at real time equipment performance data delivered via predictive maintenance software.
Using an example from Enertiv’s experience, we see that maintenance schedules can be dynamic (as opposed to time-based), data-driven and focused on the specific activities needed at that time.
All buildings with elevators have an elevator motor room on the roof of the building containing the elevator motors and electronic panels that control the elevators. These rooms normally must be maintained below 85 F, requiring A/C units. If the A/C unit is over-sized, which is common, it will cycle-on for a short period and then remain off for a long time until the temperature rises above the set temperature again.
In this example, the building began to experience elevator shut downs during the day in the summer months. One or more elevators would go offline and the building would call the maintenance staff. They would arrive, restart the A/C unit and reset the elevator from the roof control panels. The underlying cause of the recurring issue was a mystery without looking at the performance data.
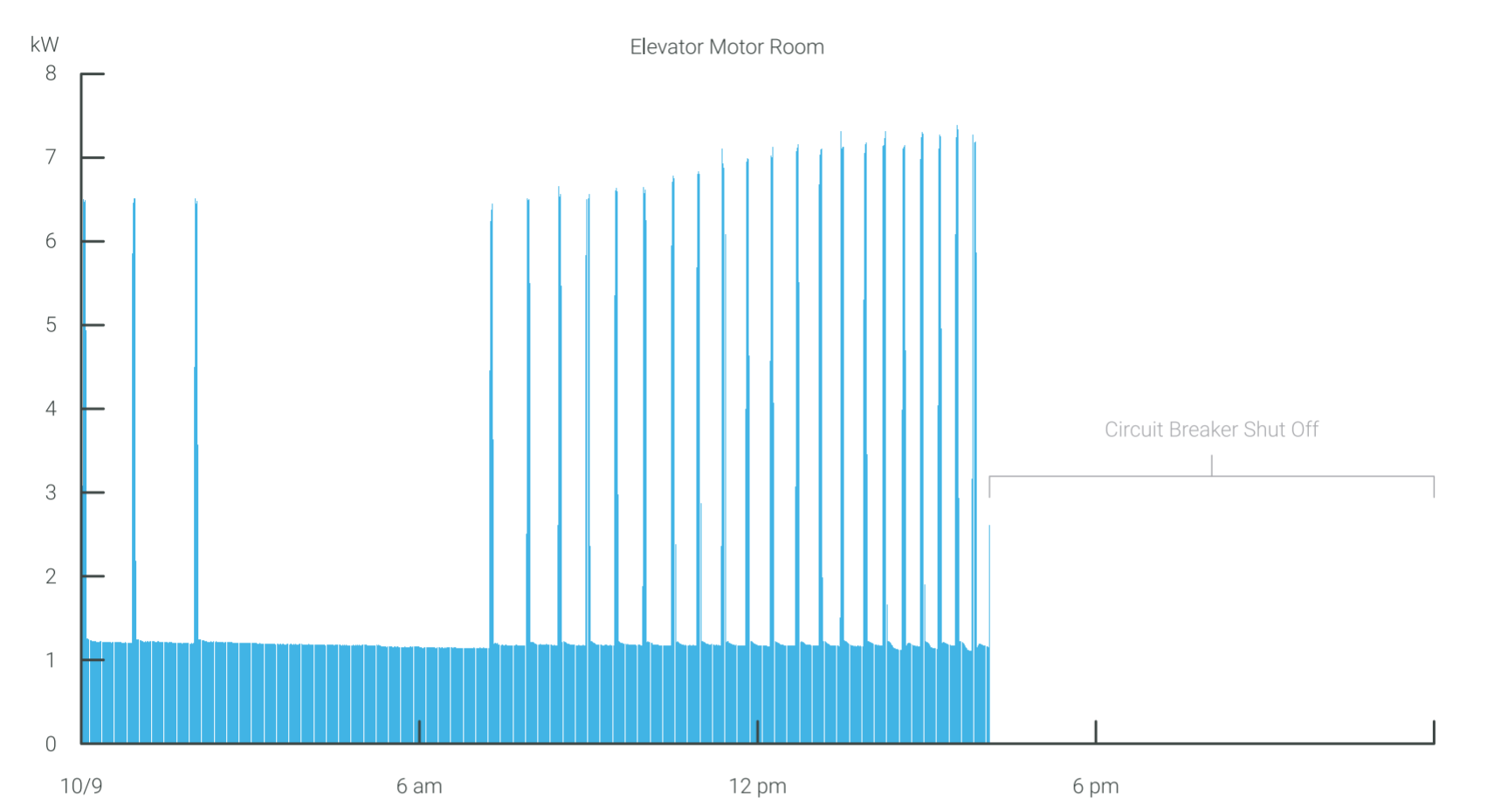
The chart above shows the load from a 7.5 Ton A/C unit spiking-on up to 7.4 kW (with a peak current of 65 Amps) and maintaining a continuous load of 1.2 kW from the fan and A/C controls. The unit was significantly oversized with the on-cycle lasting 4.5 minutes and the off-cycle lasting 25 minutes in the early morning. As the outside temperature rose during the day, the off-cycle shortened to 13 minutes with the A/C unit cycling on four times per hour. This caused the circuit breaker to overheat and shut off, turning off the A/C unit. This eventually lead to the electronics panels overheating and shutting down one or more of the elevators.
Preventative maintenance may have never uncovered this, no matter how often it was scheduled. Instead, the immediate solution was to set an alert when the power consumption fell below 0.5 kW for 5 minutes so that a staff member could quickly reset the circuit breaker for the A/C unit — avoiding an elevator shutdown. The longer-term solution was to replace the A/C unit with a smaller unit.
It’s a commonplace practice to budget money every month for repair costs but even if you do all your planned preventative maintenance, something will eventually break. When it does, unless there’s a building monitoring system in place, the root cause will remain a mystery, unscheduled emergencies will continue, and maintenance staff time will continue to be squandered.
See how Enertiv can bring data-driven maintenance to your building, helping you save time and money.