With the plummeting cost of sensor technology and the proliferation of analytics platforms to convert data into usable insights, real estate owners and operators are deploying solutions to monitor all sorts of outputs from their tenants and building systems.
Often, IoT deployments are targeted towards solving specific problems that are caused by chronic issues. Now that over 2 billion hours of data have been collected (and another 3,000 hours every minute), we can work backwards to understand the differences between asset types and seek optimizations based on a more empirical process.
For example, according to aggregated equipment performance data from Enertiv, multifamily properties have two times the number of equipment faults than do office properties. On the other hand, offices have two times the number of equipment scheduling issues compared to multifamily properties.
The point is, just as family history is used to indicate the diseases that one is susceptible to, owners and operators should know the “family history” of their building vertical to understand and properly prioritize their equipment and technology investments. Here’s what the data tells us different building verticals in commercial real estate.
Office
Office buildings are generally unoccupied from the hours of 8 pm to 8 am (not counting that one overachiever we all know and love). This means that the equipment that keeps occupants comfortable is generally operating on a regular schedule. These schedules are notoriously difficult to optimize and maintain without continuous monitoring.
Even Class A properties that have multimillion-dollar building management systems (BMS) to control when and how equipment operate are not exempt. In fact, improperly configured BMS’s are believed to account for 20% of building energy usage.
If the goal is to maximize profits while maintaining tenant comfort, owners and operators of commercial office properties should be aware that their vertical’s “family history” indicates a propensity for scheduling issues.
Leaving HVAC systems and lighting on overnight can needlessly lower net operating income by tens of thousands of dollars. Perhaps that doesn’t matter while cap rates are low, but when the market tightens and vacancy rates increase, optimizing equipment schedules can be a no-cost source of mitigation.
It’s not enough to assume that because equipment can be programmed to run on a schedule, that it is being programmed effectively. All too often settings are initially commissioned and then forgotten in a set it and forget it fashion.. To work around this, Machine learning algorithms based on sensor data can provide continuous verification against the inferred schedule of a building’s occupancy schedule based on when systems ramp up and down.
According to ASHRAE, optimizing schedules can produce 10–20% savings on baseload utility costs. Not bad for a no-cost adjustment that can be done immediately.
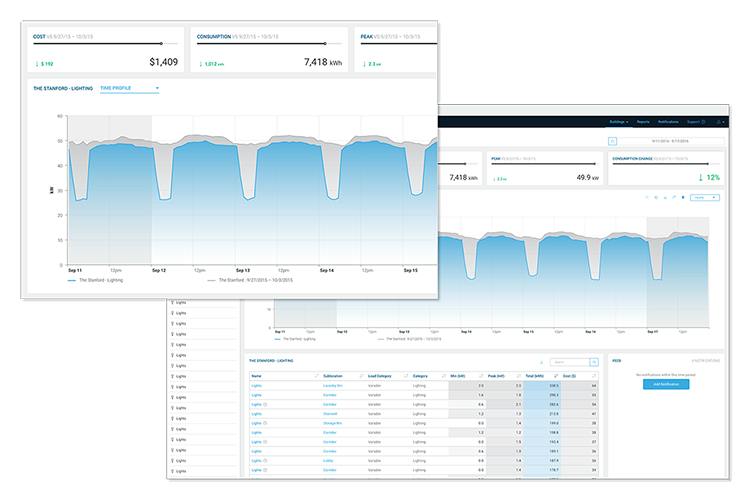
Multifamily
Unlike office buildings, multifamily assets do not have predictable schedules. Most of the equipment in these properties generally run continuously to ensure that the tenant common spaces remain comfortable regardless of the time.
While this means that there are fewer concerns about scheduling, it also means downtime can be more detrimental given the around-the-clock expectations. It also means that equipment runtime hours add up much more quickly than in office properties. This leads to a higher likelihood that equipment will be run to failure and require corrective maintenance or a visit by a third party vendor.
Ironically, systems are run around the clock to ensure tenant comfort but running to failure causes breakdowns that reduce tenant comfort far more than if routine shutdowns for maintenance had taken place.
Owners and operators of multifamily properties should be aware that the family history of their asset type indicates a propensity for expensive corrective maintenance and repairs.
Performance data tracked through sensors can quickly determine the pattern of normal operations for individual pieces of equipment. Whenever there is a deviation from the norm that indicates a failure is imminent, a notification can be sent to on-site teams to perform maintenance. This is known as predictive fault detection.
Unlike equipment schedules, where corrective action will produce savings immediately, this remediation must be measured in net present value.
Foregoing maintenance will save money today, but cost a lot more in the long run. Over a 20-year horizon, preventative maintenance has an ROI of 545%. What’s more remarkable is that predictive fault detection has a 500–1000% ROI on top of preventative maintenance!
Hospitality
From a data perspective, hospitality properties look like a hybrid of multifamily and office properties. When rooms are occupied, equipment such as packaged terminal air conditioning (PTAC) units are running constantly to ensure a comfortable stay. Unlike multifamily, occupancy and vacancy are much more fluid, but not on a regular schedule like offices.
When rooms are vacant, the indoor environment should be allowed to drift towards the current outdoor conditions to save operating costs. This rarely happens with consistency. Often, the set points for the temperature at which point HVAC units begin heating or cooling are suboptimal.
Set point issues are common across asset types but should be a primary concern to owners and operators of hospitality properties, especially when it comes to PTAC units. Given that hotel guests don’t pay electric bills, they have no incentive to be mindful of consumption.
Technology can help compensate the misalignment in incentives. Machine learning algorithms based on occupancy, temperature and electrical sensor data can determine which units are conditioning vacant spaces and wasting operating expenses.
Studies have found that optimizing the set points can produce up to 31% savings on the cost of running HVAC systems.
Industrial
Ecommerce is booming and so are the logistics and warehouse properties downstream.
Growth comes with increasing competition and the need to drive optimization at the margins. This requires a more holistic approach to data collection and analysis.
The name of the game in industrial portfolios has always been reliability. Understanding the most critical equipment for a specific tenant will inform the optimal sensor deployment.
For example, the facilities that house perishable foods need to ensure complete reliability when it comes to their industrial HVAC units. The ideal deployment would likely combine electrical sensors to track issues such as short cycling as well as leak detection sensors for refrigerant fluids.
In addition to deployments geared at ensuring reliability for critical assets, many facilities are looking to make the switch from preventative maintenance to conditions-based maintenance. Like predictive fault detection, a continuous stream of data from equipment-level sensors can help move maintenance teams from a calendar-based schedule to performing maintenance only when the data indicates it’s necessary.
Conditions-based maintenance has been shown to reduce maintenance labor costs by 25–30% over standard preventative maintenance.
Conclusion
Once it’s laid out in the data, the differences between asset types are not very surprising. Still, there’s a big difference between making a technology investment based on intuition and using empirical evidence to drive decision making.
Everyday, IoT-based technologies are gaining more traction in commercial real estate. The goal is sound: to digitize the physical infrastructure to lower the cost of running a property and create a superior tenant experience.
Like many things in life, the first step involves taking stock of your current situation and mapping out a path to what you want to achieve.
Each property will have unique circumstances, but there are some general rules based on the “family history” of the building vertical. Commercial office properties should focus on optimizing equipment schedules, multifamily properties should focus on predictive fault detection, hospitality properties should optimize HVAC set points, and industrial facilities should focus on conditions-based maintenance.
Luckily, Enertiv’s platform can optimize along all of these dimensions. Get a demo today!