Most owners and operators rely on their property management system to capture and manage tenant work orders requests, the foundation of most maintenance programs in commercial real estate.
In addition to traditional maintenance activities, many portfolios have, to some extent, deployed real-time monitoring to track potential issues related to critical infrastructure and the indoor environment.
However, these two types of technology are usually divorced, resulting in limited value generation.
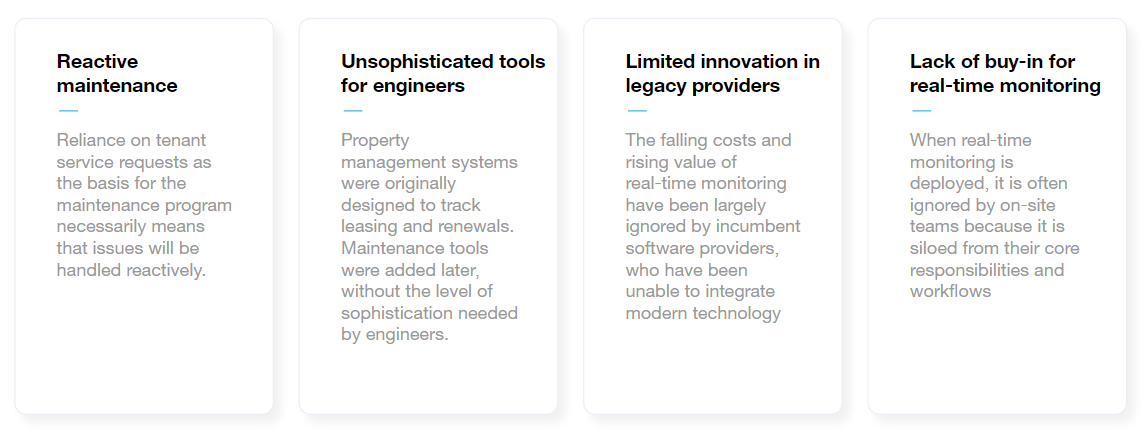
In order to maximize the value of technology, the human factor needs to be considered.
The primary issue when it comes to maintenance is that incumbent providers do not meet the needs of modern owners and operators and, at the same time, the value of real-time monitoring is not being realized because of the siloed, disparate nature of those solutions.
Why combining work orders and real-time monitoring matters
Just two reasons:
#1: Most maintenance programs are wasting time and money
Obviously, tenant-based maintenance requests are important. Digitizing this workflow has reliably produced a better experience for tenants and a more manageable process for operators.
However, tenant-based maintenance requests are necessarily reactive. In some cases, that’s okay; it’s more cost effective to react to small items like burnt out light bulbs than to try implementing a preventative program.
But when it comes to issues like hot/cold calls, elevator shutdowns and other issues related to critical infrastructure, by the time a tenant is complaining, what was once a small issue has become a big problem.
For example, a boiler that is short cycling will continue to operate and provide heating and hot water to tenants. That is, until the unnecessary wear and tear causes it to break down.
Relying on tenant service requests means that the issue will not be recognized until it is serious. When this happens, operators spend a lot of time responding to complaints and dealing with third party repair vendors. Likewise, the repair often costs ten times what preventative steps would have.
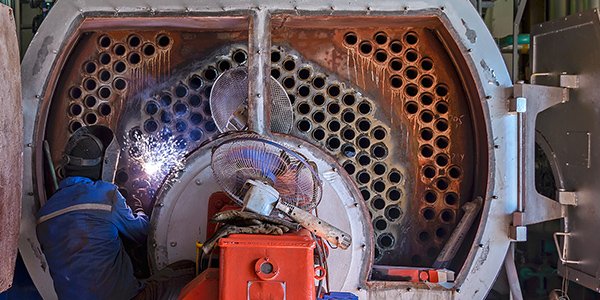
The problem is that once this cycle is in place, it’s very difficult to break out of.
Responding to emergencies results in deferred maintenance elsewhere. Deferred maintenance leads to more emergencies and so on.
#2: If real-time monitoring is deployed outside of core workflows, it will be ignored
One way out of the cycle of deferred maintenance is to be alerted to small issues the moment they occur, so they can be addressed and the downstream effects of larger problems can be avoided.
That is the job of real-time monitoring.
Whether the issue is a short cycling boiler, a pipe leak, or long term degradation of mechanical equipment, timely alerts can ensure corrections are made before tenants even notice, saving time and money.
However, real-time monitoring is often considered a separate type of technology, unrelated to the core responsibilities of inspections, work orders and preventative maintenance.
There may even be a complete disconnect around who is onboarded onto the monitoring software. Too often, the solution and the onboarding are geared towards energy managers, controls experts, and systems engineers.
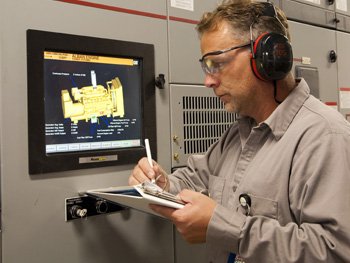
While those are important stakeholders, this disconnect is one of the biggest reasons that alerts go ignored, issues go unaddressed, and the value of monitoring remains limited.
The building operators, technicians and engineers are the front lines for correcting issues. Even when they are included in onboarding, it’s often seen as an additional thing to learn and pay attention to, when they don’t have enough bandwidth to complete what’s already on their plate.
Why the combination is more powerful than the sum of its parts
In order to maximize the value of technology, it must meet every stakeholder where they are.
First, it’s important to recognize that the core competency of property management systems is on revenue management and accounting.
Tailoring a software experience for operators that goes beyond tenant work orders and also digitizes their inspection checklists, asset tracking and vendor management, goes a long way towards creating buy-in and improving outcomes.
And if that same app is where real-time alerts appear and are resolved, you can count on adoption.
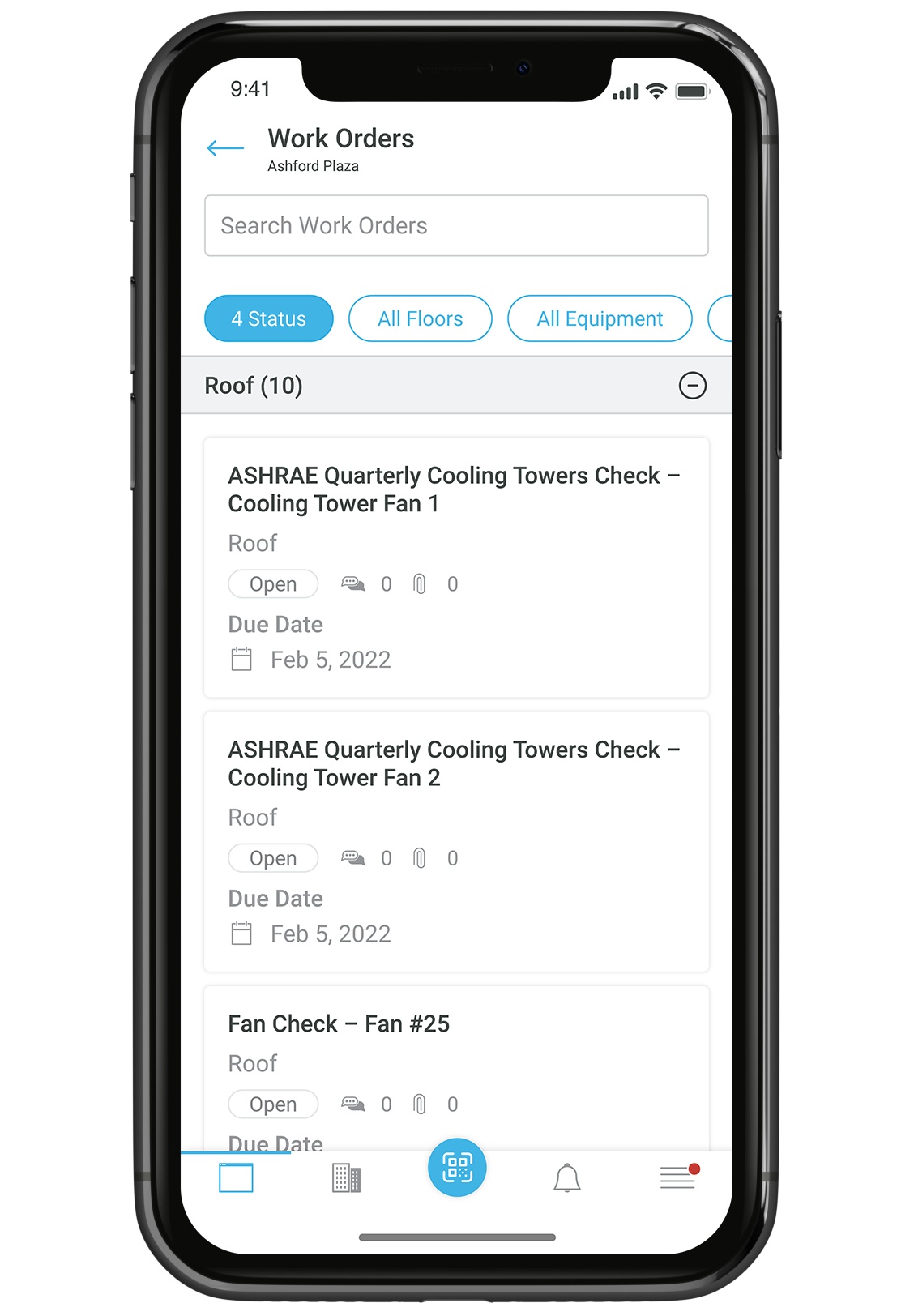
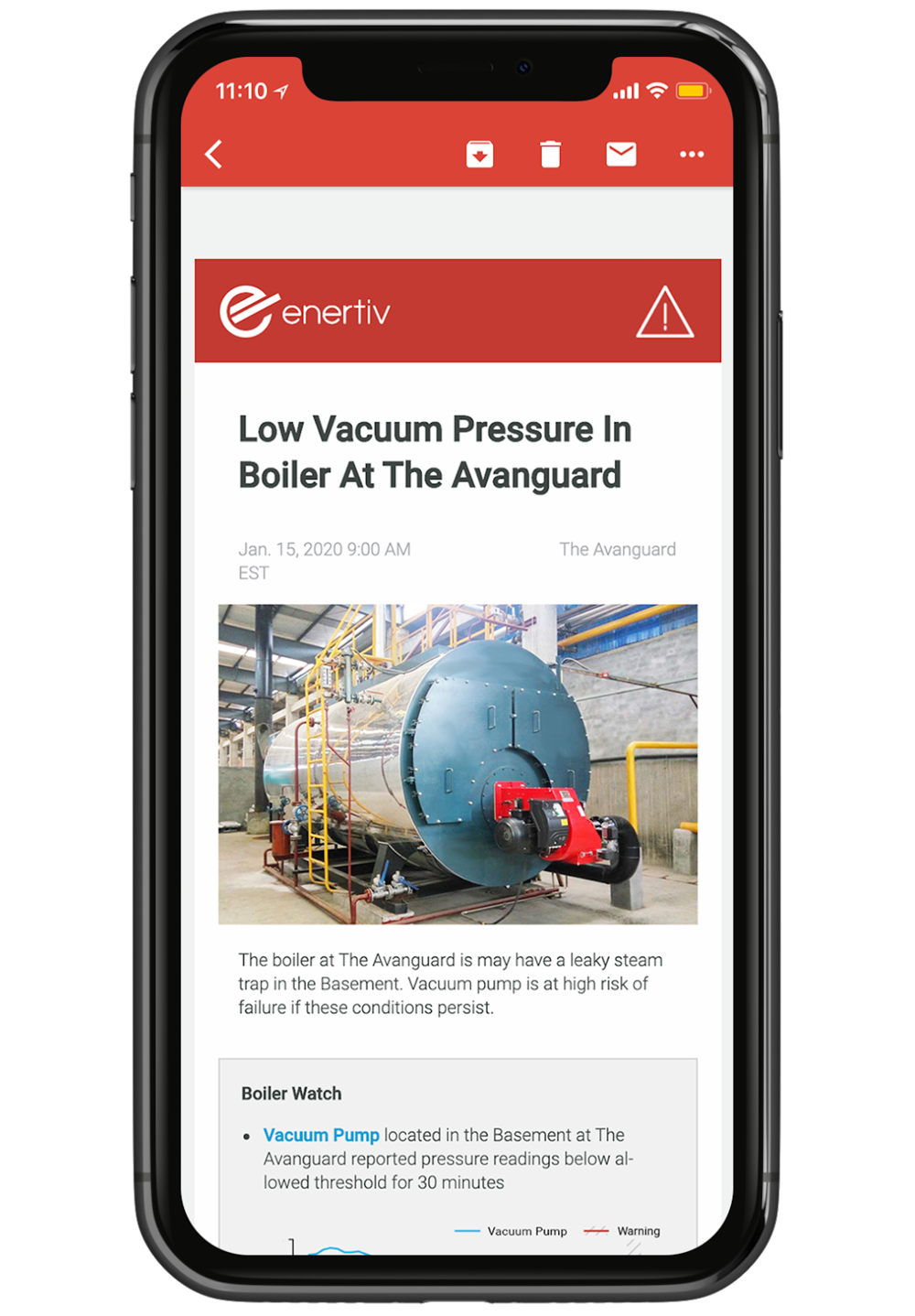
But that is just the beginning.
Real-time monitoring can also be translated into runtime hours. This allows preventative maintenance schedules to be refined based on how much equipment is actually being used, rather than a static calendar.
Likewise, operations teams can hold third party vendors accountable by getting notified exactly when they start working on equipment, and how long they spend.
Because all of this is data is consolidated, asset managers get visibility into how time is being allocated, where work orders are originating from, and how the asset is performing from an operational perspective.