It’s that time of year again. The days are getting shorter, temperatures are falling, and building operators are bracing for a host of winter-related challenges. Unpredictable events such as frozen pipes bursting or boilers breaking down are all but guaranteed. The only problem is that owners and operators don’t know when or where.
The disruptive and costly problems that come with cold weather often put operators between a rock and a hard place. Either they can deploy manpower to monitor every property, or they can sit back and hope that nothing bad happens. The tradeoff is whether the cost of deploying the extra resources is worth being able to respond more quickly to problems once they do occur.
Luckily for today’s operators, there’s still time to deploy technology in targeted ways to proactively guard against these issues. Real-time data from IoT devices and sensors can monitor potential problems more effectively than human senses can and enable managers to deploy resources dynamically.
In fact, with the right sensors and a software backend to digest and analyze the data, just about any problem that keeps operators up at night can be continuously monitored at a much lower cost than that of raw manpower.
Here are a few examples of how data can make this winter easier (and less expensive!).
Frozen Pipes
One of the biggest concerns for owners and operators during winter months is the prospect of pipes freezing and bursting. While the building’s interior provides insulation for most of the infrastructure, sometimes the outside air intake will flow right past pipes and dramatically increase the likelihood of pipes freezing.
Even the best run portfolios in the world have been perplexed by this problem. Sadly, the best solution to date has been to deploy technicians to monitor the pipes daily at every building.
The repair and damage costs of a pipe burst are high, so this is a worthy tradeoff. But an hour of an operator’s time is the most valuable resource managers have. Salaried time spent checking for frozen pipes is time spent away from critical preventative maintenance, potentially solving one problem while creating others elsewhere.
In reality, the time spent on this work is often overtime, which significantly increases the cost of intervention. To make matters worse, human senses are simply insufficient to prevent issues before they occur. The extra costs in this case serve only to mitigate the amount of damage that occurs.
While having operators at every site in case of emergency is better than nothing, some portfolios are opting to deploy low-cost wireless temperature sensors to track when pipes are close to freezing. This way, interventions can be performed before a pipe freezes and managers can deploy their teams in a smarter and more efficient way.
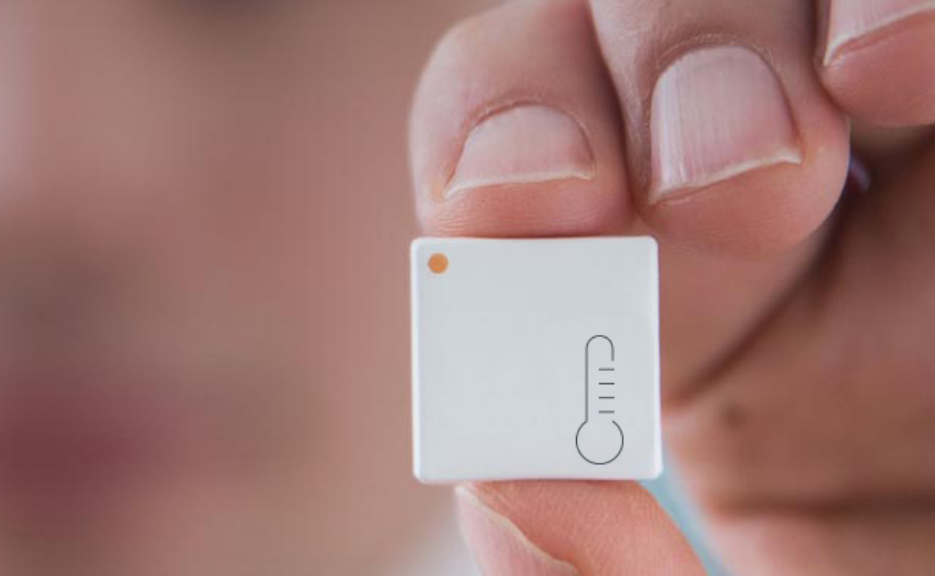
Boilers
Tenants fully expect that there will be consistent heating and hot water during the winter months. Unfortunately, many properties still rely on boilers that are decades old, under maintained, and unreliable.
The first step to ensure maximum uptime for a boiler is to perform consistent preventative maintenance. However, given that only 13% of commercial real estate properties have robust proactive maintenance programs in place, this is likely insufficient advice for this coming winter.
One thing that can be done immediately is the deployment of a package of sensors to track the various inputs and outputs of a properly functioning boiler.
Complex systems such as boilers can fail for a number of reasons. Leveraging sensors to track electrical demand, water levels, flow, and pressure can identify, and even predict when a fault is going to occur.
Not only does this ensure that tenants remain warm and comfortable, but it also can be done at a fraction of the cost of running the system to failure and paying for a third part repair.
Interruptible Gas Program
In some regions, the utility offers building owners the opportunity to purchase gas at a lower cost provided they are willing to switch to oil on particularly cold days when supply is tight.
One example of this practice is in Con Edison’s Interruptible Gas Program in New York. While the program is a great way for operators to save money on gas costs, the penalties for non-compliance are severe.
Any gas used during the period specified by the utility will be charged at nine times the market rate for the first infraction. The second infraction leads to an immediate loss of compliance and a reversion to market rate for ongoing consumption.
With the stakes so high, and communication from the utility notoriously sparse, many owners and operators are deploying technology to ensure their compliance. Sensors placed on the gas meter can be tied to software to guarantee that no gas is used unintentionally.
Any building that is enrolled in the Interruptible Gas Program in New York or any similar program elsewhere would be wise to ensure their compliance with real-time, verifiable data.
Indoor Air Quality
Cold air holds half as much moisture as hot air, leading to a significant drop in humidity levels during the winter. With far fewer chances for natural ventilation, the building’s ventilation equipment is depended upon heavily to ensure tenant comfort and a healthy indoor environment.
The first step to having an easier winter is to continuously commission the performance of rooftop exhaust fans to ensure that fan belt issues and motor problems are identified immediately and resolved before tenants notice.
Fan belts slip off and snap all the time. The repair is simple and inexpensive, but often remains undiscovered for weeks without real-time performance data.
Poorly ventilated spaces contribute to symptoms — such as headache, fatigue, dizziness, nausea, cough, sneezing, shortness of breath and eye, nose, throat and skin irritation — of a condition called sick building syndrome (SBS). The economic costs of SBS in under-ventilated buildings are significant and far exceed the energy-related cost savings.
In order to verify the effectiveness of ventilation, a number of portfolios are also deploying air quality sensors in tenant spaces. While this may not be worth the investment in every scenario, this is a requirement for achieving the WELL certification, which is becoming more and more important to tenants and is trending towards widespread adoption
Conclusion
Winter is quickly approaching. While there is a host of known challenges associated with operating buildings in cold weather, technology has created opportunities to handle problems elegantly and at a lower cost than that of the prevailing alternative.
There are enough areas of responsibility in a building operator’s job description; activities like checking for frozen pipes, reacting to tenant complaints, and verifying compliance should be avoided when possible.
The idea is to modernize the conventional approach to building operations without scrapping it entirely – integrating cutting-edge sensor technology with big data and predictive analytics to make problem solving more proactive and intuitive.
It's not too late to winter-proof your property with sensors. Get a free building survey today!