Introduction
Real estate asset managers are charged with cultivating market value, mitigating risks, and making smart investments to increase returns for ownership. Notably, they do this work within the broader context of the company’s portfolio and the overall market conditions.
On the other hand, building operators are responsible for ensuring that equipment critical to a functional property run consistently and efficiently. In most cases, decision making for these duties occurs in a vacuum, without much knowledge of what is happening in the greater portfolio.
This is not the fault of operators, asset managers have the benefit of dealing with information that is relatively easy to gather, organize, and analyze. It’s only recently, with data made available from Internet of Things (IoT) sensors, that operations teams have been able to get transparency into their assets without physically being there.
And just in time too. With rising competition and rental revenue progression flattening or declining in most markets, real estate companies are putting more pressure on building operators to generate value through cost savings. In response, operations teams are adopting technologies to streamline their processes and eliminate waste wherever possible.
But there is a ceiling to the benefits of optimizing each asset as a singular effort. Beyond the low-hanging fruit of optimizing equipment configurations for efficiency purposes, deep cost savings require distributing labor and material resources in an intelligent way. Without the ability to simultaneously understand the conditions on the ground in each building across a portfolio, operators cannot act holistically.
That is where “digital twin” solutions come in.
Digital twins take many different forms, but the essential elements are a digital visualization of a physical asset and some form of data about that asset. The manufacturing and construction industries have used digital twins for some time to simulate different scenarios before executing on expensive and irreversible decisions.
For building operators, digital twins haven taken on a different form. Operators do not have the luxury of simulating different scenarios, they must make decisions on the fly as issues arise. The real-time data from sensors enables them to do just that, without being on site, and within the context of the broader portfolio.
Here are some specific examples of how digital twins can help operators to act more like asset managers.
Decision Making
When equipment breaks down, as it inevitably does, operators must triage the severity of the issue. Priority is generally given to issues that directly affect tenant comfort, especially if a particularly angry tenant is actively voicing their displeasure. This may or not be the right decision at the time, but without data, it’s simply impossible to know.
There is plenty of research around the high costs of deferring maintenance. Most operators know this, but the reality on the ground is never so black and white. Operators must quickly prioritize tasks and determine whether the issue can be fixed by on-site operators, requires support from more experienced operators within the company, or needs to be outsourced to a third-party vendor.
Having a digital twin of each piece of equipment on site allows portfolio-level managers to quickly pull up the history of faults detected on that piece of equipment. If there have been numerous breakdowns and a series of “band aid” fixes to get the system back up and running, it may be determined that a full servicing from the vendor is necessary.
On the other hand, when issues could be fixed internally but there isn’t the technical know-how on site, digital twins enable more experienced operators to troubleshoot with staff remotely. Not only is the real-time data and condition of the equipment available, but also digital versions of O&M manuals, spec sheets, and other documentation that is usually non-existent or buried somewhere in the engineer’s office.
Oftentimes, the most difficult thing about doing maintenance is getting the right person with the right parts in front of the right machine. Digital twins allow operators to make better decisions so that they can optimize their maintenance and repair activities.
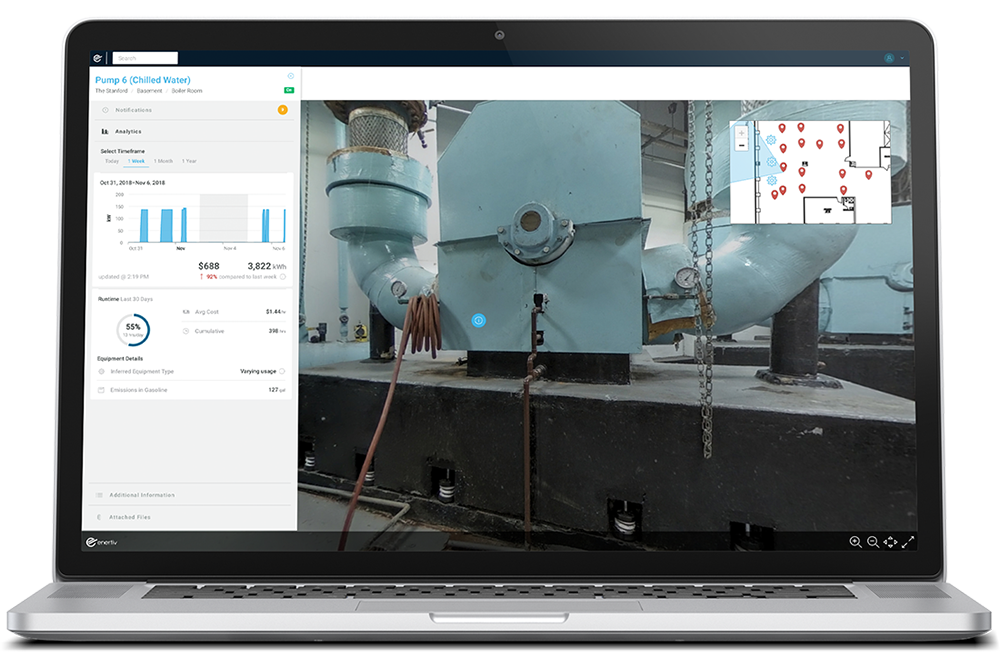
Allocating Labor Resources
In addition to the extra demands being placed on building operators, not having enough resources to carry out existing responsibilities was listed as the most common concern in a recent survey conducted by Building Operating Management.
With fewer resources, allocating staff properly across a portfolio becomes critically important. As mentioned before, digital twins can reduce the travel time necessary for operations managers to help solve problems on site. This directly saves costs and allows them to work on more valuable tasks.
In addition to saving travel time, digital twins enable operators to accurately measure performance indicators like mean time to repair (MTTR) and mean time between failure (MTBF). With granular data into the performance of on-site teams, staff can be shifted to more appropriately match the needs of each property.
When staff is shifted, digital twins can reduce the costs associated with training and onboarding operators for a new property. Before the individual ever steps foot on site, they can know exactly where critical equipment is located and what the most common issues are.
Allocating Material Resources
When budgeting season rolls around each year, there are usually 50 different things that could be replaced in a building. Asset managers evaluate investment options based on expected cash flows and returns. But operators often submit their needs based on what causes them the biggest headaches, which may or may not be the costliest problem and best deployment of resources for the portfolio.
To make matters worse, the difficulty of predicting when equipment will need to be replaced tends to bunch large expenditures into the same year, the bane of every asset managers’ existence. There may be a replacement schedule based on the manufacturer’s expected useful life of equipment, but these are rarely as accurate as real estate companies would like.
Digital twins can be used to benchmark equipment performance across the portfolio, thus allowing operators to submit capital investment decisions based on the true operating expenses and lifetime cost of different makes and models. Smoothing out capital investments and making decisions on long-term cash flows is truly thinking like an asset manager.
Conclusion
Digital twin technology is all about bringing physical assets into the digital world. There are obvious benefits such as reducing operating expenses and serving as a central documentation repository. There are also less obvious benefits such as enabling building operators to think and act with complex financial considerations in mind.
When an operator leads the discussion by talking about the net present value of one decision over another, they are much more likely to get fully funded by management. The more that activities can be framed by the cash flows that they generate (or save), the more valued the operator will become in the eyes of ownership.
Going a step further, understanding the detailed financial considerations opens the door for building operators to align better with the goals of the portfolio. By understanding the investment objectives that led to the acquisition of the properties they operate, they can look beyond the physical confines of those assets to assess where they sit in the market and make recommendations in line with defined financial goals.
Enertiv's digital twin technology is the first in commercial real estate to combine real-time data and a digital 3D environment. Schedule a demo today to see how it works.