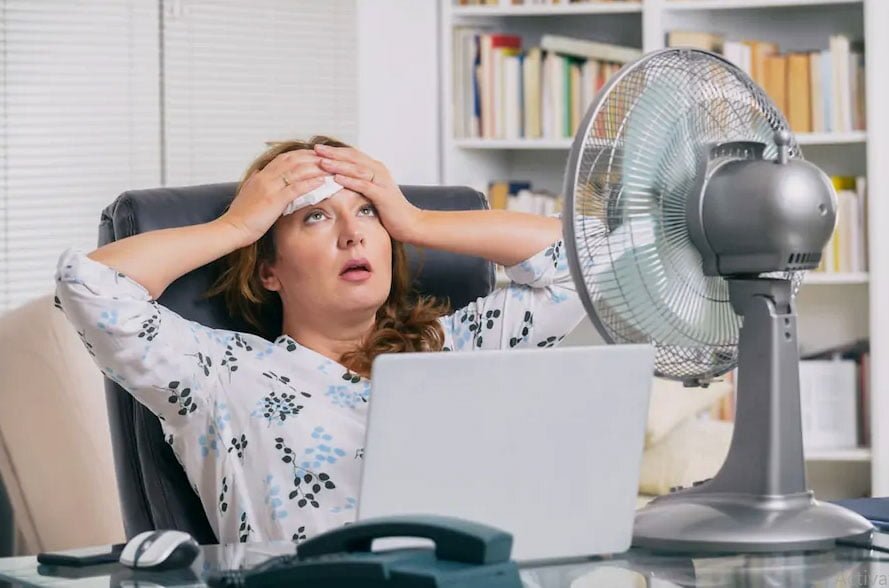
It's 7:34 am on a Tuesday when the first call comes in.
Caroline, a go-getter, has shown up to the office early to find that it’s unbearably hot. She thinks "I commuted for this, when I could've worked at home?"
The property manager relays the complaint to the building engineer, Chad.
There are 12 air handling units in the property and dozens of reasons any one of them might not be functioning properly. Despite being relatively common, issues like this can easily turn into a full day affair that pushes back critical items like budgeting and planned preventative maintenance.
But Chad knows the building inside and out. He springs into action, grabs his tools, and heads to investigate the specific air handling unit that serves this tenant's space.
As suspected, the refrigerant is leaking due to a damaged line. He shuts down the system, makes the repair, and is able to get it working before the rest of Caroline's colleagues arrive between 9 and 9:30 am.
Download Now: Fault Detection Saves 30 cents per square foot of potential waste
The problem is, Chad is close to retirement…
A larger trend
The truth is, an entire generation of engineers retiring is one of the existential crises facing the commercial real estate industry.
The pandemic isn’t helping either. Workers are now leaving the labor force due to retirement at twice the rate they were pre-pandemic.
If this weren’t bad enough, it’s combined with a dearth of workers to replace them.
In Chad’s 26 years, he’s seen many younger operators come and go. Some made it to decision making positions and wouldn’t get their hands dirty anymore. Many more have left for other industries or ended up bouncing around from property to property.
Finding operators isn’t easy either.
83% of commercial real estate companies report feeling the strain from a lack of skilled workers. The result is that portfolios are 22% understaffed on average and the lead time to hire a new operator is around four months.
It doesn’t stop at recruiting and hiring. Keeping them around is becoming more challenging too. 40% of building services professionals state that they were unhappy with their salary to the point it could precipitate a job move.
Adapt or die
The real danger of the Chad’s of the world leaving a property is the institutional knowledge they take with them.
Chad knows where the valves are that don’t appear on any riser diagrams. Chad knows how the complicated spreadsheet for submetering tenants works. Chad knows which equipment is prone to what failures.
What all that adds up to is a property that is one person leaving away from everything falling apart. It wouldn’t be the first one.
It’s not Chad’s fault either. The job is so demanding of one’s time that the idea of taking a step back to document processes, update infrastructure specs, and set up digital repositories of information is a non-starter.
So, what is an owner-operator grappling with this existential crisis supposed to do?
There is some promise in smart buildings that can automate much of the operational decisions in a building, especially around HVAC usage.
But someone still has to turn the wrenches in the building. That job is not going away anytime soon.
It’s just that that “someone” will be younger, less skilled, have less experience, and be more likely to change jobs.
To adapt to that reality, there needs to be a process to get anyone with a basic set of skills to be able to hit the ground running.
The Trojan Horse
We need to get Chad’s experience and knowledge into the cloud, so it can be accessed by anyone who comes after him.
The question is how, since the reality of having no time outside of core responsibilities still remains.
The answer is a Trojan Horse.
The only way to do this successfully, especially at scale, is to give Chad a tool that he actually finds beneficial to his daily work, despite the fact that he’s generally resistant to changing what has worked for him for decades.
The key is simplicity.
When building a mobile maintenance solution, there’s a natural tension between the user and the manager. The user wants things to be as simple as possible. The manager wants as much data as possible, which usually adds complexity (and time for the user).
For example, let’s take a maintenance checklist. It would be much simpler for the checklist to say “inspect all air handling units.” There might be 12 AHUs, but the engineer only has to mark off one task.
Now, a manager would much prefer for each of the 12 AHUs to be separated and in fact have specific checklist items for how to “inspect” them. He’d also want to know what floor those AHUs are on, their make/model, installation date, expected replacement date, schedule, etc.
Demo Now: The Enertiv App Maintenance Module
So, how do we bridge this gap?
It’s not easy, but it can be done with the combination of asset tagging that automatically digitizes nameplate information and documentation, an enormous library of checklists tied to specific equipment makes/models, a user-friendly mobile app, a team of experts focused on engineering first (as opposed to property management first), and smart software that even the Chad’s of the world find benefit in.
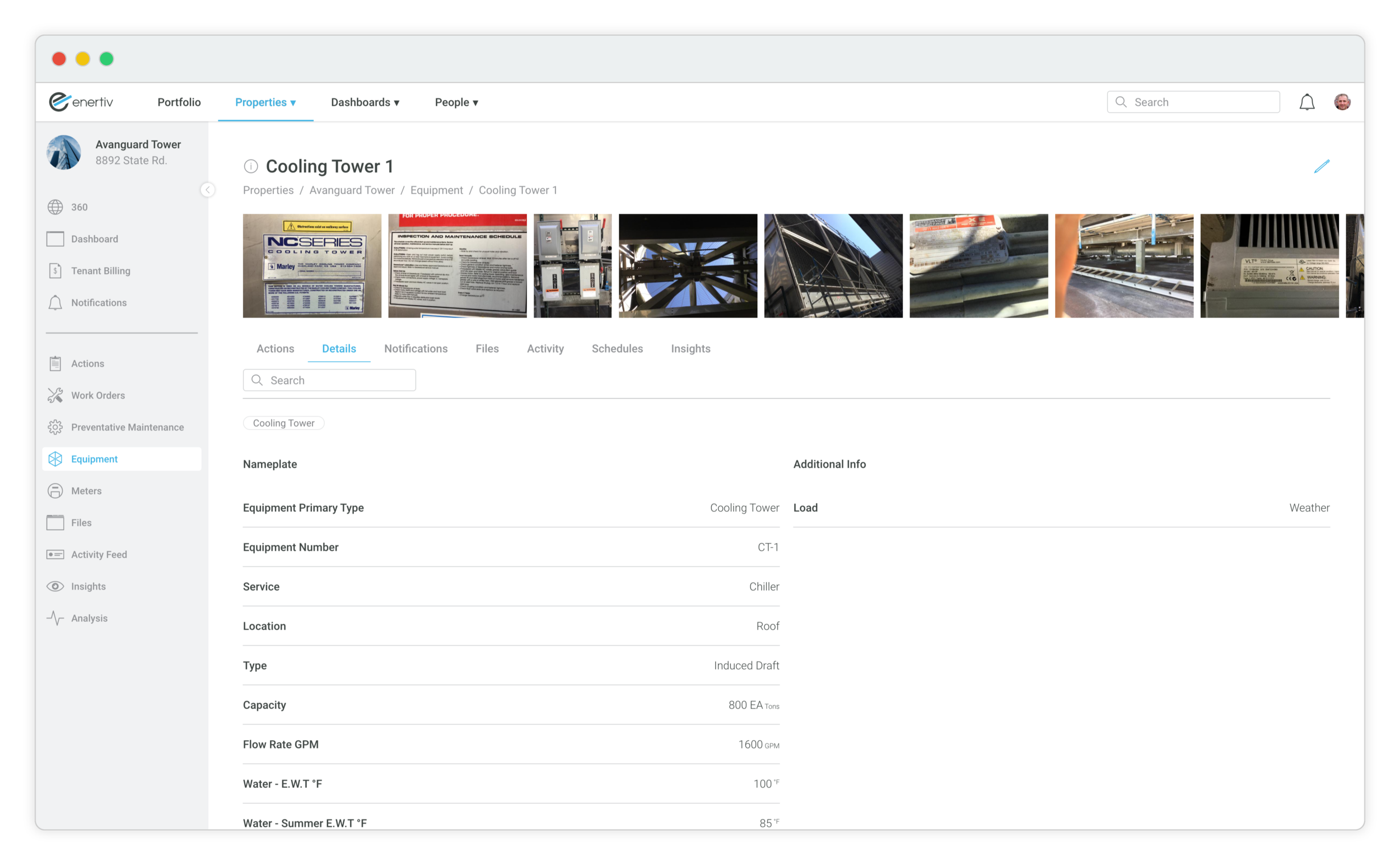
What this does is to significantly reduce the “setup” usually involved in adopting a new technology, while simultaneously being granular enough to support reporting and provide a real blueprint for anyone who comes after Chad.
To take it a step further, this system can be integrated into the BMS and other sensors so that Chad’s ability to diagnose the root cause of issues can be carried on, even when his replacement doesn’t have the same level of knowledge or experience.
The same integration can calculate runtime hours, so the preventative maintenance schedule can be optimized based on usage instead of static calendars. Layer on a digital twin and training can occur asynchronously and remotely, thus meeting the challenges and expectations of tomorrow’s workforce.
Instead of fretting over a trend that can’t be controlled, it’s more productive to accept the reality and, in doing so, recognize what a gift it is to still have experienced engineers. All that’s needed is alignment so their gifts can be immortalized with technology.