A great irony persists when calculating the return on investment for Internet of Things (IoT) technologies in commercial real estate: The value of the IoT lies in the data it generates, but to calculate this value exactly, data are required.
For once, it is not enough to simply say that the real estate industry is slow to adopt new technology. There are inherent aspects of the business that make exact calculations difficult. For instance, while there is a direct correlation between equipment downtime and lost production (thus revenue) in manufacturing, tenants generally pay the rent in full regardless of how critical equipment performs.
This truth is a double-edged sword however. While a broken boiler doesn’t directly affect revenues for the duration of the downtime, constant issues or lengthy interruptions can contribute to expensive vacancies. In other words, the margin of error is high in the short term, but the risks are also higher in the long term.
Because of the indirect relationship between building performance and net operating income, important metrics have not been tracked sufficiently, nor baselines created. This makes understanding the relationship between IoT investments and returns a guessing game, ultimately justifying the slow adoption of technology at portfolio scale.
Establishing a Baseline
According to data from the Building Owner and Managers Association (BOMA), costs related to maintenance and utilities account for 48% of non-fixed operating expenses. These numbers alone do not tell a compelling story however. Though a significant percentage, it’s not clear to many owners and operators that investments in the IoT will produce enough savings to create attractive return.
Many IoT solutions to date have focused on energy because the savings are much more direct than in maintenance and repairs. The moment you correct an operating schedule, retrofit old equipment, or configure a system to use resources more efficiently, the cost savings will begin to accrue in a measurable way.
Thanks to benchmarking regulations and years of effort from organizations such as the American Council for an Energy-Efficient Economy (ACEEE), best practices in building operations have been shown to cut energy consumption by 10–20%. In fact, a Department of Energy study found that to realize the same benefits, equipment retrofits cost approximately 20-times more than low-cost operational measures.
More and more, commercial real estate portfolios are coming to recognize good energy management as simply one aspect of good overall management. Real-time data from IoT devices are not just feeding “energy dashboards” anymore, the focus has shifted to delivering specific, actionable insights.
A perfectly tuned building will see energy efficiency degrade by 10–30% each year. To combat this, IoT-based solutions notify building operators if equipment is running outside of normal occupancy hours, is set to an inefficient sequence, or could be shifted to other times to lower peak demand charges. This not only ensures that the 10-20% of energy savings are realized, but that they are maintained going forward.
As a concrete example, we can look at two 200-ton centrifugal chillers serving a 162,930-square-foot office building. IoT data revealed that many hours were spent with both chillers operating simultaneously at less than 45% capacity each. The analysis showed that savings of about 5 percent could be achieved by operating a single chiller at 90% load instead of both at 45% load. Annual energy savings would be about 34,500 kilowatt-hours (kWh), or about $2,800 per year at $0.08 per kWh.
Further analysis revealed additional savings. By shutting down one chiller, the auxiliary chilled-water and condenser-water pumps that served it could also be shut down. This would yield additional savings of about 14,100 kWh or $1,100 annually, bringing the overall savings from improved chiller sequencing to about $3,900 per year.
But there are multiple non-energy benefits of implementing IoT solutions, many of which are more strategic and interesting to decision makers than mere energy cost reductions. In fact, despite being the single largest line item on total operating expenses, energy savings are not the main source of long-term value derived from the IoT.
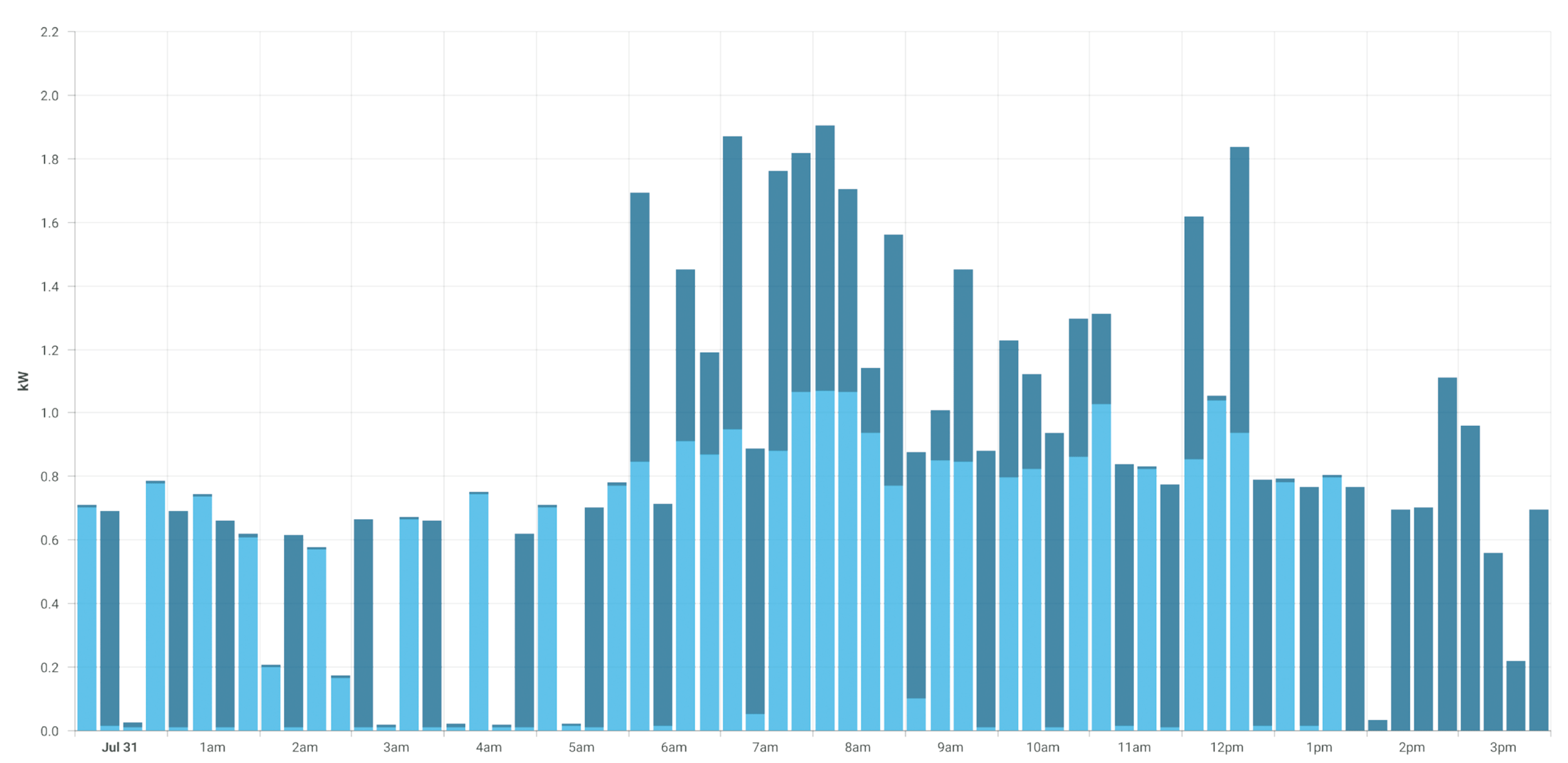
Calculating Non-energy Savings
To calculate the true value of the IoT, we need to be able to put specific dollar amounts to the cost of maintenance, the cost of reactive repairs, and the added cost to equipment replacements without proper maintenance.
Data compiled by Jones Lang LaSalle helps us do just that. To exemplify this value, we’ll look at one of the 200-ton centrifugal chillers from the previous example using the following assumptions:
- The chiller is 10 years old
- The time horizon is 25 years
- The discount rate (return earned when money is invested elsewhere) is 10%
- Inflation is 3%
- Repairs cost 3X that of maintenance ($16,500 per repair)
- Repairs will be necessary every three years without proper maintenance
- Repairs will be necessary every four years with proper maintenance
According to the data, it will cost $1,000 per ton, or $200,000 total, to replace the chiller. With proper maintenance, which will cost $5,500 per year, the chiller will need to be replaced every 23 years. Without proper maintenance, there will be lower maintenance costs, but the unit will need to be replaced every 15 years.
In the maintenance scenario, the chiller will need to be replaced in year 13. With no investment in maintenance, it will have to be replaced twice, in year five and year 20. Comparing the two scenarios shows that the investment in maintenance on the chiller has a relative net present value (NPV) of $44,880!
Of course in real life, chiller maintenance is not a simple yes or no. More often, there is a preventative maintenance schedule based on the manufacturer’s recommended schedule that is followed some percentage of the time.
In the same way that data from IoT sensors can be leveraged to determine strategies for energy savings, data can be used to create a more dynamic maintenance schedule. Instead of performing maintenance on a calendar-based schedule, IoT data enables conditions-based maintenance, where upkeep is performed only when data indicates a need.
Building operations are very hectic and calendar-based maintenance is often skipped because there are urgent repairs that take priority. However, a Department of Energy report found that by taking a conditions-based approach to maintenance, repairs become easier, simpler and cheaper by up to 90%. Conditions-based maintenance also helps eliminate critical malfunctions by up to 75% and enables the building to plan repairs for a more convenient time.
There are multiple ways to monitor the “condition” of equipment in real-time. Vibration and temperature sensors have been deployed for decades to continuously monitor the health of equipment. More recently, IoT devices that track the energy consumption at the equipment-level have become a primary source of data collection.
There are a few advantages to energy consumption readings for driving non-energy savings benefits. First, the other sensors mentioned need to be placed individually in each piece of equipment, whereas energy-based devices can be placed at the distribution panel to track many building systems from one place (also conveniently avoiding the issue of sensor battery depletion by drawing power directly from the panel).
The second advantage is that energy consumption readings provide a full picture of equipment performance. Instead of simply noting whether equipment is in normal temperature or vibration parameters, energy consumption readings can be translated into equipment runtime hours. This is a key variable in developing preventative maintenance schedules, so replacing guesses and assumptions with hard data can prove extremely valuable.
Finally, energy-based IoT data collection can serve to feed an entire building monitoring system, encompassing both energy savings and maintenance improvements. It may not make financial sense to place a temperature or vibration sensor in smaller equipment systems such as ventilation fans. But because a group of fans may be fed from the same circuit panel, these systems can be included in the IoT investment.
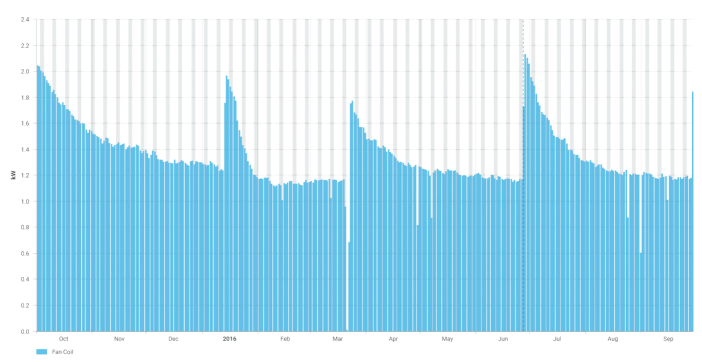
Conclusion
The benefits of proper maintenance and maximum equipment lifespan is inherently more difficult to quantify than energy savings. Moreover, the disconnection between equipment downtime and lost revenues have resulted in a dearth of benchmarking data for the commercial real estate industry.
Nevertheless, as the potential for a market downturn increases and real estate companies begin to focus on cost savings to drive net operating income, maintenance and equipment reliability should not be ignored.
By now, most real estate owners and operators have heard about the IoT and the “Smart Buildings” that it can enable. But many have also realized that the obvious benefits can be difficult to quantify as bottom-line value.
There is still a lot of room for improvement in developing industry-wide benchmarks for metrics such as maintenance costs and equipment reliability, but it’s important for those evaluating IoT technologies to remember that the value of the IoT is not limited to what can be easily measured.
As more portfolios adopt the IoT, and data becomes aggregated, these metrics will become illuminated, and even more important metrics, such as the relationship between building operations and leasing decisions will finally become attainable.
If you’re interested in a building survey to begin to determine the value of an IoT investment for your building or portfolio, you can request one here.